三动拉延模结构特点及调试过程
文/刘佳一·长春创元模具设计有限公司
本文通过对某车型行李厢外板三动拉延模的结构特点进行分析,介绍三动拉延模的调试重点,阐述理论设计推动实际调试生产的作用和重要性。
汽车冲压件要通过落料、拉延、成形、修边冲孔、翻边整形等多道工序的冲压工艺才能完成。拉延工序是汽车冲压件产品成形的第一道工序,通过拉延模具在压机上将平板料冲压成具有产品基本形状的制件,在合理的冲压工艺的基础上,拉延模结构设计及调试研配是汽车冲压件实现成形要求的重中之重。
拉延模一般采用单动拉延、双动拉延、三动拉延和切角拉延等模具结构形式。本文以行李厢外板为例,阐述三动拉延模结构特点及调试过程。
三动拉延模的结构特点
产品内外均有压料区域、压料力大、拉延稳定、成形效果好,适用于拉延形状复杂、产品有较深的凸、凹型面、拉延深度比较深的覆盖件。按其实现的功能主要分两种结构形式,一种是靠设备实现的三动拉延(图1),即在双动的基础上,利用设备的拉伸垫在下模也使用压料圈的结构形式。另一种是靠模具结构实现的三动拉延,主要通过模具结构本身的功能设计实现三动拉延效果,跟压床实现的结构完全不同。
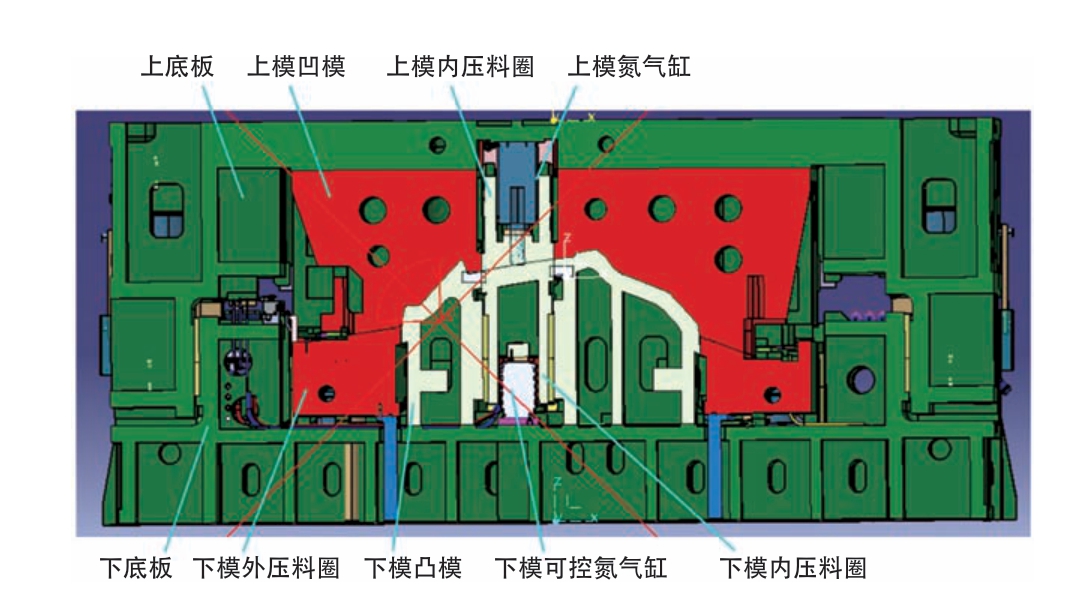
图1 三动拉延模结构剖面图
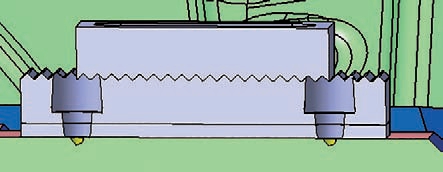
图2 锯齿形平衡块

图3 快速定位
靠模具结构实现的三动拉延分两种形式,一种是在双动压床上,没有下气垫,在上凹模中设计压料板,用氮气缸控制压料行程。另一种是上模带有外压料,上模压料圈不是在外滑块上,而是靠氮气缸先压料,靠模具结构实现三动拉延。第三种是下内压料圈使用可控氮气缸,此结构是在单动拉延基础上,下模窗口处增加内压料圈,内压料圈使用可控氮气缸;在上模凹模里增加活动压料圈,使用氮气缸施加压力,用于提前凸模压住板料,利于拉延成形,靠模具结构实现三动拉延。这种结构是上下都有活动结构形式,一般用于后行李厢外板等汽车冲压件模具。
结构设计主要原则
⑴导向。基本部件包括:凸模、下模内、外压料圈、下底板、凹模、上模内压料圈、上底板。三动拉延模常用的结构导向形式是压料圈与凸模之间采用内导向,上下模具之间采用上底板与压料圈导向。
⑵分体结构。高档车型或生产批量大的拉延模的凸模、凹模、压料圈材料常常选GGG70L,这种材料相对费用较高。为了节省材料费用,结构上通常采用分体结构,凸模与下底板分开,凹模与上底板分开,采用螺钉固定、明键或暗键为主要的定位方式,将拉延凸模安装在下底板上,拉延凹模安装在上底板上。一般情况下,为了便于车间装配,在客户允许的情况下,凸模与下底板的定位尽量采用暗键形式。
⑶平衡块设置。由于三动拉延模的活动部件较多,在下模外压料圈板料外均设置锯齿形平衡块(图2),来增强活动部件工作时的稳定性,改善模具工作时由于侧向力而引起的受力不均衡的问题。
⑷干涉检查。现在主机厂为了加快生产节拍,实现连续高效无间歇,绝大多数采用自动化送料方式,即在自动冲压生产线采用机械手送料。所以模具的干涉检查是对自动冲压线进行动态仿真模拟,是制件通过性分析的一个重要阶段,能模拟出设备在生产中的运行状况,结构设计员在设计过程中及时发现模具的碰撞干涉问题并予以解决。
快速换模的设计要素
快速换模是模具快速装换调整的一种方法,是现代工业自动化生产中必不可少的过程,也是实现柔性化生产的必要手段。在模具设计时,充分考虑快速换模的设计要素,为快速换模做好准备。
⑴考虑快速安装定位结构,可以显著地缩短和设定模具安装时间(图3)。
⑵迭代车型的不同处采用镶块替换,便于快速拆装及更换,且处于最小浪费的状态(图4)。
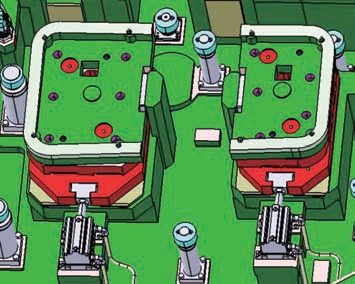
图4 镶块替换
⑶下模的全托杆躲避孔设计,可以免除压床托杆拆卸(图5)。
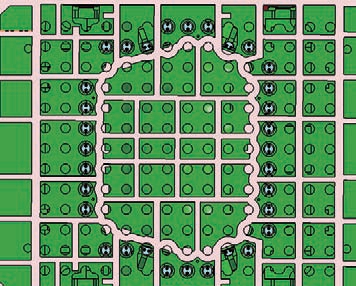
图5 全部托杆躲避孔设计
⑷利用手动或气动切换装置控制DCH 孔的冲裁,既实现冲孔工艺,又保证型面及冲孔质量(图6)。
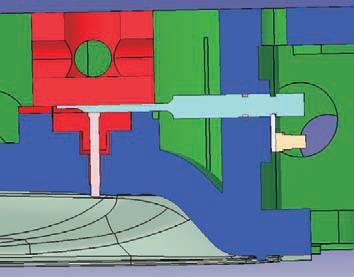
图6 手动切换装置
⑸上模安装射频芯片,要求无遮挡,便于天车识别,将模具起吊并快速放置到压机的正确位置,实现快速安装(图7)。

图7 射频芯片安装位置
三动拉延模的调试
⑴影响和难点。
由于模具结构上下模都有活动结构,上模的凹模、上压料圈及上底板;下模的凸模、下压料圈及下底板都有直接或间接的导向连带关系,一般情况下,由于加工及装配的累积误差等原因,在调试期间经常要先消除一些异常影响和累积误差,所以装配精度及导向精度的控制及调整是满足调试工作的前提。
⑵准备技术文件。
调试阶段要有理论数据及文件的支撑,所依据的主要技术文件有:CAE 分析模拟报告(图8)、理论着色图(图9),还需要加工后的ATOS 扫描报告、调试记录卡、压机挠度补偿数值及区域图作为调试参考信息。
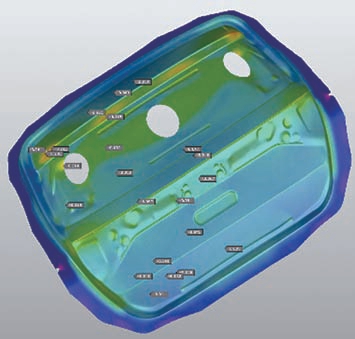
图8 变薄率分析
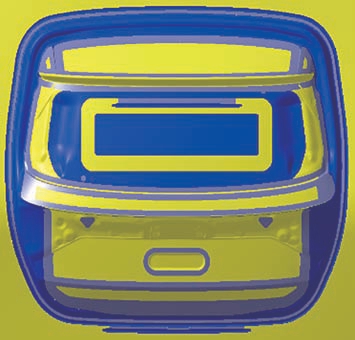
图9 理论着色图
⑶凸、凹模基准确认。
用油石检验淬火区域平整度,油石沿45°方向运动,在运动过程中要始终覆盖淬火区域。用研板涂蓝色轻推凹模压料面筋内侧管理面,确认平整度,如不平需用砂轮机精修,油石推顺,800#砂纸抛光,最后再次确认。
⑷功能认证及首次压件。
三动拉延模的活动部件较多,所以导向精度是功能认证的基础和关键。导向间隙要求控制在0.05mm以内。调试前检查导向间隙是否合理,将上、下模导板涂蓝色,检查导向间隙,合模查看着色状态;主要导向的合模状态达到要求后,再检查其他部件的导向间隙,导向间隙满足要求后,再在拉延筋内外侧压料面上钻孔压铅丝,测量压料面间隙。
首次压件时要分次压,根据制件特点至少分三次到底。制件成形50%时,检查和分析制件开裂问题;继续压到成形80%,根据制件的成形情况,如果开裂严重,需要采用降低压料力或垫塑料布等辅助手段来缓解或减轻制件开裂问题的产生;压出完整的100%到底的件,针对制件开裂和起皱的区域对制件修整,即调试时板料两面刷蓝色,蓝色涂层一定要薄,目的是准确找到硬点。压至制件开裂,根据着色状态调整筋外侧30mm 以外硬点,根据开裂区域,筋内侧不动,外侧适当调整,主要调整凹筋的凸R,优化局部压料状态(图10)。
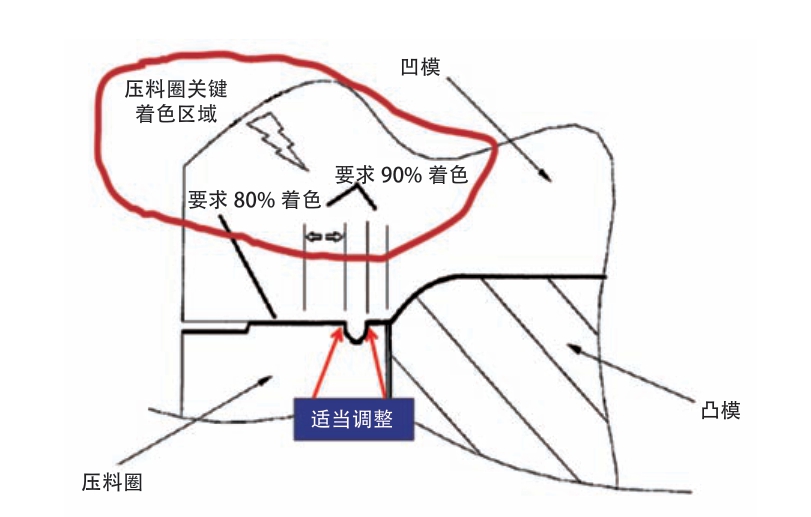
图10 压料圈凹筋的凸R 调整
⑸压料圈的研配。
压料圈着色的目的是因为拉延模需要良好材料流入控制。为了达到要求,研配时不带平衡块,用压料力的30%,研配压料圈着色。拉延件不能有缩颈、褶皱和开裂。筋内侧与筋外30mm 着色达到90%,30mm 以外区域着色达到80%。只有压料面的研配状态和表面质量好,才能达到成形时材料流动状态良好,实现成形工艺要求。
⑹研修凹模前提条件及研配方法。
当能得到一个完整的拉延件时就可以研配凹模,凹模研配对于是否能得到良好的尺寸和面品至关重要。通过着色确认凹模表面硬点。拉延件双面刷蓝油,把拉延件正确放置在凸模上,使用低于理论成形压力30%的压力压制凹模着色,移开拉延件,通过着色查看到两面的硬点。
⑺去除硬点。
如果硬点干涉量在0.5mm 以上,则需要在低压力状态下,用砂轮机以45°交叉方向打磨;如果硬点干涉量在0.5mm 以下,在低压力状态下,用400#油石以45°交叉方向蹭除硬点(图11)。
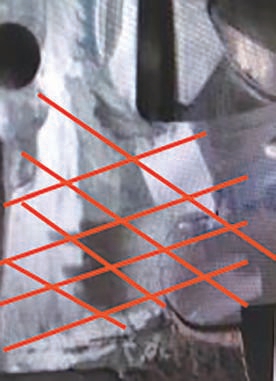
图11 蹭除硬点方向
⑻用理论成形压力压件。
移开拉延件,可以看到双面还会残留硬点,再逐渐去除。当着色达到90%时(图12),用400#至1000#砂纸抛光,逐步优化接触状态以达到良好的成形状态。最终研配完成时,需要达到理论着色要求,即要求着色区域需达到95%,其他区域需达到80%。需要注意的是:一个拉延件不能使用超过5 次,多次使用板料会变薄。
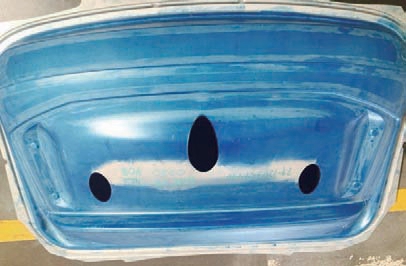
图12 着色件
结束语
本文针对行李厢外板三动拉延模的结构特点,阐述了生产调试过程的重点及注意事项,保证生产中能够全面根据设计的理论调试参数逐项确认实施,推动调试阶段快速满足产品成形性、间隙及着色、尺寸精度等各项要求,为三动拉延模的设计及调试提供有效途径。
刘佳一
长春创元模具设计有限公司设计员,主要从事汽车覆盖件的拉延、修边、冲孔等大型模具结构设计工作。
本文通过对某车型行李厢外板三动拉延模的结构特点进行分析,介绍三动拉延模的调试重点,阐述理论设计推动实际调试生产的作用和重要性。