多工位压力机在家电领域的应用
文/臧崇运,司大强·江苏兴锻智能装备科技有限公司
随着环保政策的深入及工业4.0 时代的来临,工业加工制造产品的精密化、轻量化、集成化越来越高,对材料利用率、能源消耗、环境污染和产品性能、成本、生产周期的要求愈发严苛。为此家电行业、汽车零部件等企业逐渐对旧设备、旧的生产工艺进行淘汰,升级、推广新工艺新技术,特别是对中小零件逐渐由多机联线的手工生产线提升为单机多工位自动生产线。本文就兴锻多工位的研发及其在家电、汽车零部件领域的应用进行介绍。
多工位发展历程
第一代单机联线多工位生产线
皮带轮是发动机中常用的零件,采用3 ~4mm厚的SPHD 材料毛坯,成形难点在于带轮底部要进行增厚,底部中间圆柱的壁厚是料片厚度的1.5 ~2 倍。皮带轮的传统成形工艺是铸造、焊接、拉深成形。使用传统成形工艺生产的皮带轮通常尺寸精度不高,机械性能较差。多道次拉深成形工艺取消了焊接,可以提高产品尺寸精度,同时在多次拉深的过程中,材料变形硬化效果累加,有助于提高强度。多道次拉深成形一般有12 ~14 道生产工序(图1),具体工艺流程为⑴落料→⑵一次拉深→⑶二次拉深→⑷三次拉深→⑸冲孔→⑹四次拉深→⑺五次拉深→⑻六次拉深→⑼翻边→⑽一次镦厚→⑾二次镦厚→⑿三次镦厚→⒀四次镦厚+整形→⒁外缘翻边。单机联线生产时,第10 到12 工序可以合并成一道冷挤压镦厚成形,使用一台较大吨位的冷挤压冲床成形。
依据现有模具,对现有设备加以升级改造,由手工生产线改造为自动化生产线。本生产线由四台AIDA 单点开式压机(NC1-80、NC1-150)、一台AIDA 冷锻压机(L1C-630)、两台兴锻单点闭式压机(ZXM1-2200、ZXM1-1600)、五台兴锻单点开式压机(ZXK1-800)等共12 台设备组成(料片为线外单独落料),这是兴锻发展历史上的第一代多工位生产线(图2)。

图1 皮带轮工序分布图
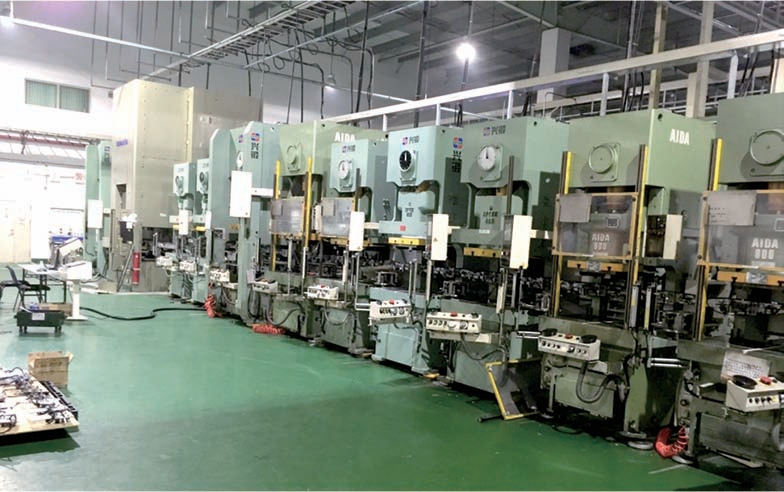
图2 单机联线多工位生产线
采用多机联线加工时,若一台设备出现问题,则会导致整线停止,维修保养比较难,影响生产效率,并且所需要的厂房占地面积比较大,人员参与度比较大,模具的开发费用和制造费用比较高。
第二代单机多工位生产线
为提高生产效率,降低故障率,考虑一机多用,即:由1 台压力机取代14 台压力机,采用多工位形式,并针对该零件提出了第二代加工工艺,即锻冲复合成形工艺。从生产效率上讲,多工位压力机的应用缩短了生产流程,减少80%人力,人均生产率提高4 倍。兴锻生产的变频单机多工位压力机如图3 所示。
第三代伺服单机多工位生产线
规模化的生产需要稳定的质量来保障效益。随着劳动成本的提高,自动化、智能化的需求越来越高,加之对资源和环境因素的要求,市场展示了对伺服多工位压力机的需求。我公司借鉴学习了日本的伺服直驱压力机技术,并实现了规模化和标准化生产,伺服电机同传统电机相比,能够提供更精准的控制,在驱动技术、节能环保、精确控制等方面有巨大优势,由伺服马达驱动的压力机,压力直接由伺服马达的扭力输出转变而成,其低速大扭矩伺服电机和齿轮直接驱动,减少了中间环节,确保传动的可靠性和效率,电机的最大峰值扭矩60000Nm、400rpm,驱动器最大电流3320A、额定功率550kW。通过伺服技术和多工位技术的应用,我公司伺服多工位压力机具有自动化、智能化、操作安全、冲压件综合成本低、劳动生产率高、制件质量高等特点,能够满足客户大批量生产的需要。
特殊超大型伺服压力机的传动主要包括:伺服电机、高速轴、中间齿轮、中间齿轮轴、偏心齿轮、低速轴、连杆、滑块。伺服电机布置在机架的后侧,布置方式为左右式;高速轴与伺服电机连接,高速轴与中间齿轮啮合,中间齿轮安装在中间齿轮轴上,中间齿轮轴与偏心齿轮啮合,偏心齿轮安装在低速轴上,连杆大端安装在偏心齿轮上,连杆的小端与滑块连接。
该伺服压力机杆为四连杆机构,其动力源由伺服电机提供。减速机构采用齿轮减速。为保证工件冲压加工精度以及设备力学特性的要求,在满足两伺服电机运动的主从关系和控制之间的反馈以及电气同步的同时,外加一级齿轮传动实现机械同步,在保证电机同步的同时需要机械同步,传动结构如图4 所示。实物照片及伺服电机布置如图5、图6 所示。
兴锻以大吨位伺服压力机产业化和国产化为目标,完成了大吨位伺服压力机的多电机同步驱动技术,解决了机身的高精密制造工艺及装配技术、控制系统、关键零部件的技术难题,制造出系列智能多工位伺服压力机,建立了智能伺服压力机研发平台。伺服多工位多应用在需要拉深及冲锻复合成形等领域。
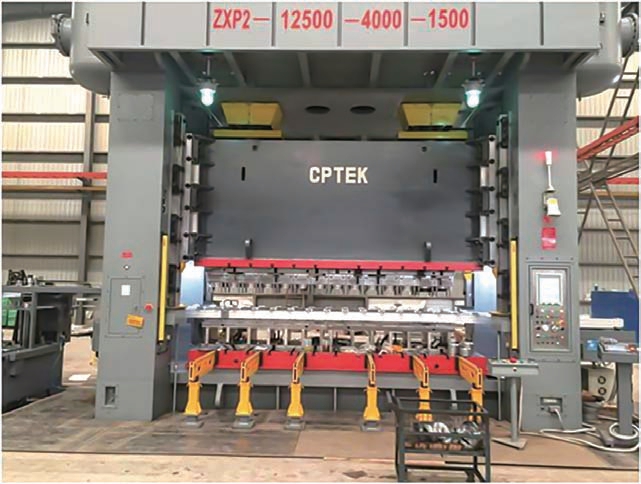
图3 变频单机多工位压力机
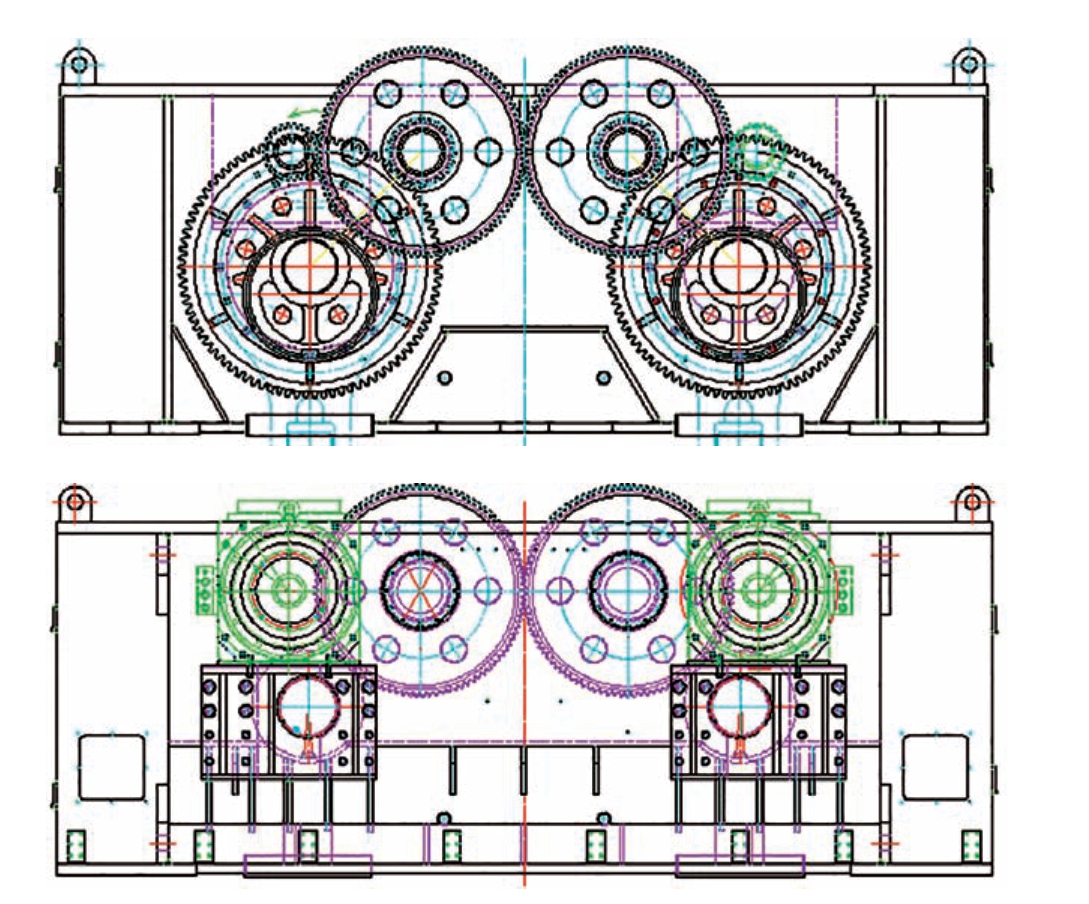
图4 双电机伺服传动结构图
多工位配置及比较
单机联线多工位生产线与单机多工位生产线相比较,在生产效率、人员数量、占地面积等方面都有一定劣势,二者比较见表1。
目前,第三代伺服多工位因成本较高,在国内尚处于推广阶段,第二代单机多工位因其生产效率高、综合成本低等优势在家电市场及汽车零部件市场得到普遍应用。
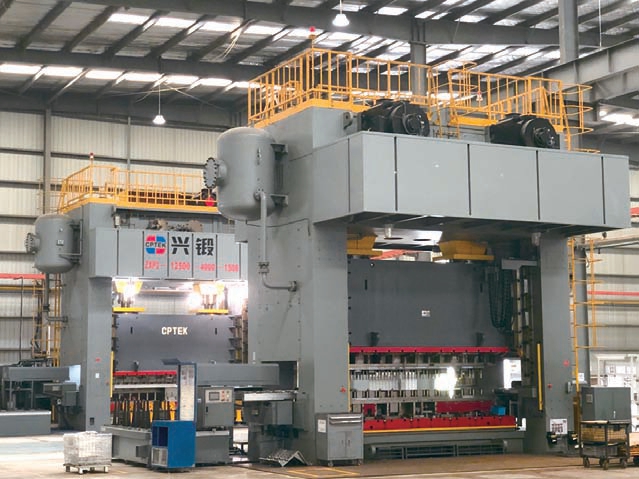
图5 伺服单机多工位生产线
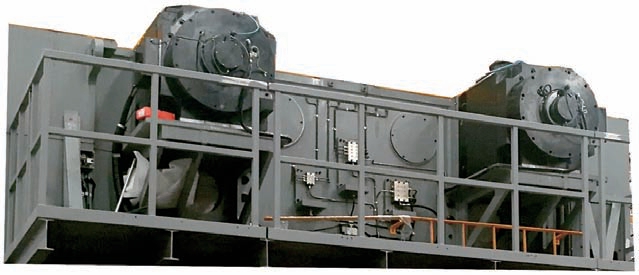
图6 伺服双电机具体布置
兴锻多工位特点及应用介绍
兴锻开发单机多工位压力机之初,就基于伺服技术,制定了高标准、开放的研发原则,形成了兴锻的技术特点:
表1 多工位配置及比较
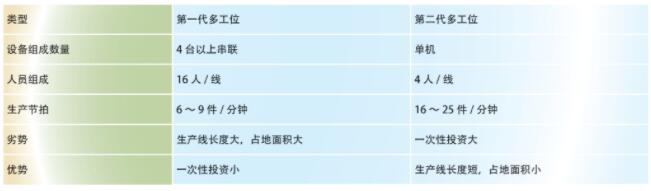
⑴开发效率更高、便于精准控制的传动系统,研发中大吨位压力机动力结构及动力传输关键技术,便于伺服控制切换。
⑵开发高刚度、高精度机身,解决机身的高精密制造工艺及装配技术难题,并开发油温油量自动检测及强制润滑系统、加压瞬时吨位的即时测定装置,提高压力机的整体精度和运行可靠性。
⑶进行金属成形工艺装备集成创新,设备与自动化同步研发。可依据客户需求同步开发工艺、设备、自动化成套生产线,主机、自动化集成控制,节约反应时间,提高生产效率。
⑷研究装备柔性、智能化的控制技术、数据管理技术,实现工业以太网通信、智能生产管理和服务。
在家电行业的具体应用案例
⑴方太专注于高端嵌入式厨房电器的研发和制造,其生产设备要求智能化、自动化,为此兴锻依据其产品批次多、生产转换频繁的特色,研发了柔性高的自动化生产线,便于快速换模,产品易切换,实现了智能控制,与方太的智能生产管理系统直接对接,提高了整个公司的生产效率。
该生产线由6 台ZXM2-2500 设备和机器人组成,设备配置为闭式双点压力机,最大行程为300mm,换模方式为换模台车,换模时间为8 分钟,生产节拍为8 件/分钟,如图7 所示。
⑵图8 所示的佳森生产线是电视机背板专用生产线,零件种类少,生产量大,为此,在研发之初,综合考虑客户工艺需求,同时研发自动化方案,采用机械臂自动化生产方式,提高了其生产效率。
该生产线由600t(1 台)+500t(1 台)+400t(4 台)设备和机械臂组成,设备配置为闭式双点压力机,最大行程为380mm,换模方式为换模台车,换模时间为10 分钟,生产节拍为6 件/分钟。
⑶为了提升生产效率,格力引进了高效的三次元冲压生产工艺,兴锻依据该工艺要求,开发了高刚度、高精度机身,解决了机身的高精密制造工艺及装配技术难题,特别是开发了中大吨位的传动系统,传动效率高,精度提升,同时预留伺服接口,为后续伺服升级改造提前进行技术准备,如图9 所示。该生产线技术参数见表2。
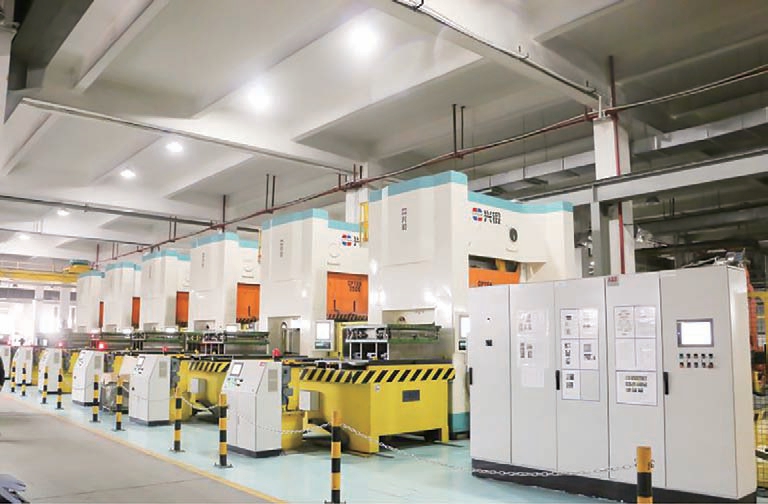
图7 方太生产线
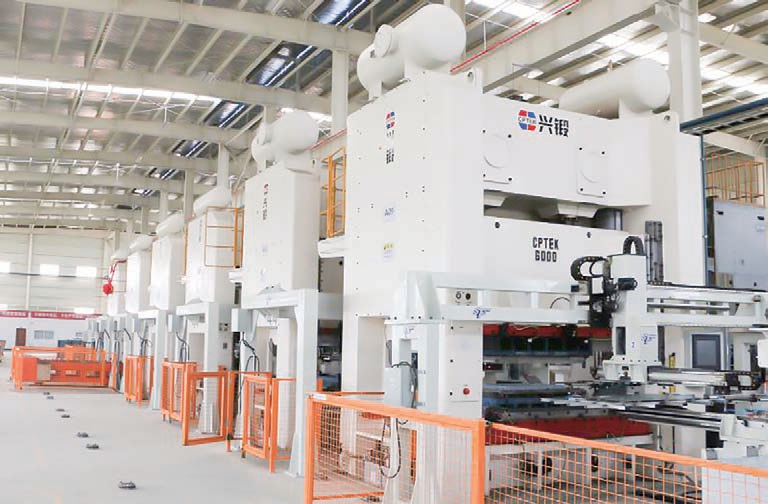
图8 佳森生产线
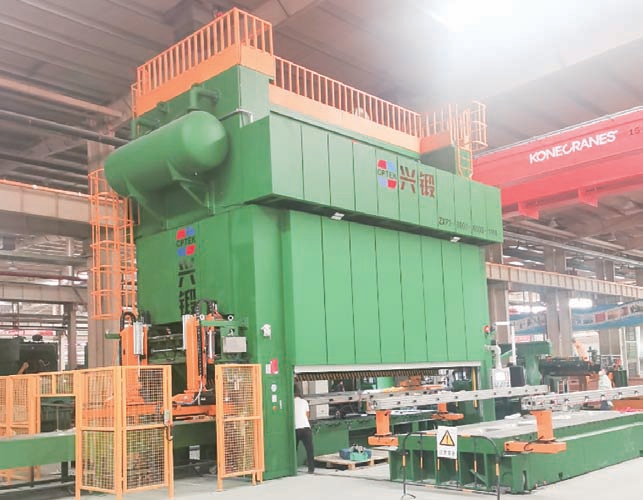
图9 格力生产线
表2 设备技术参数
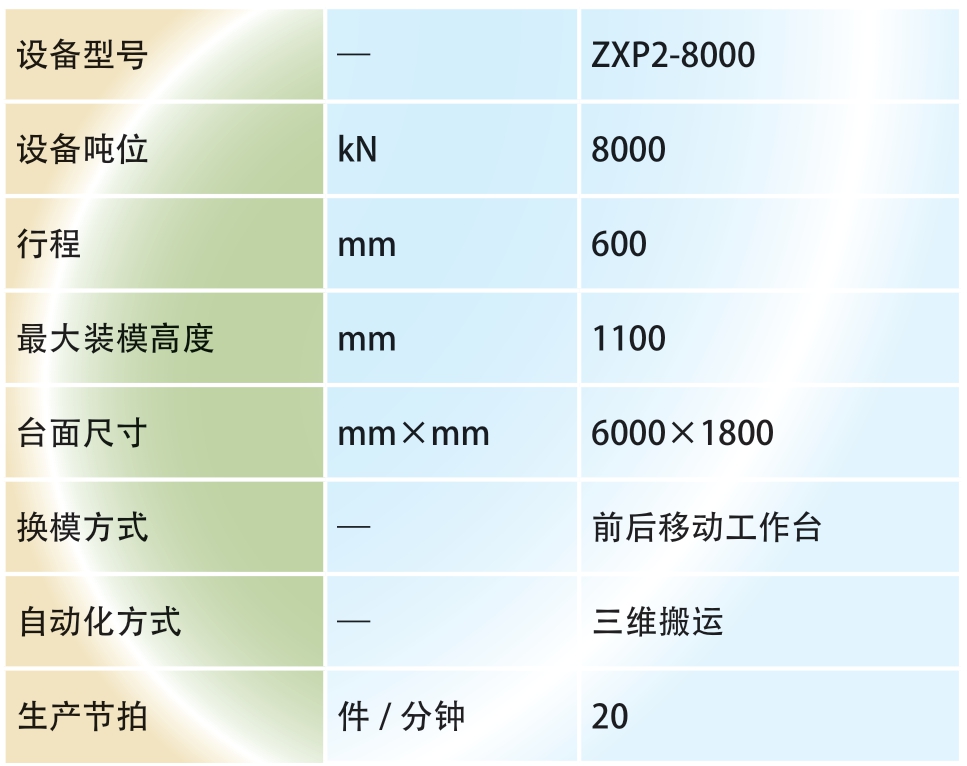
结束语
本文就兴锻开发的多工位发展历程及应用状况进行了介绍,希望给家电及汽车零部件厂家及同行一些发展启示,为我国的装备行业发展探寻出路。
随着环保政策的深入及工业4.0 时代的来临,工业加工制造产品的精密化、轻量化、集成化越来越高,对材料利用率、能源消耗、环境污染和产品性能、成本、生产周期的要求愈发严苛。为此家电行业、汽车零部件等企业逐渐对旧设备、旧的生产工艺进行淘汰,升级、推广新工艺新技术,特别是对中小零件逐渐由多机联线的手工生产线提升为单机多工位自动生产线。本文就兴锻多工位的研发及其在家电、汽车零部件领域的应用进行介绍。