冲压自动线车门外板废料利用工艺分析及应用
文/金键,寇兆阳,高洪雷,张文波,王项钧·一汽解放汽车有限公司
针对车门外板材料利用率低的问题,进行了车门外板利废工艺分析。通过从利废零件确定、利废零件及车门外板工艺优化、废料在线自动收集、利废零件调试等方面的努力,实现了车门外板窗口废料的再利用,提高了材料利用率、降低了生产成本。该方案创新性的实现了废料直接用于生产,无需二次剪切,减少了板料划伤;创新性的实现了废料的在线收集、自动堆垛,提高了自动化水平和劳动效率。
汽车驾驶室的零件中有大量的金属冲压件,冲压件成本主要包括:材料费、加工费、设备工装摊销费、人工费、运输费等,其中材料费占冲压成本的60%以上,因此提高冲压件材料利用率对于整车降成本意义重大。目前提升冲压件材料利用率的方式有:优化产品结构、优化落料排样、废料利用,采用成双、浅拉延、套裁工艺等多种,其中废料利用是将被切除的完整废料回收、用于其他零件生产的方式。废料利用能够大幅提升材料利用率,尤其是针对自动线大型覆盖件废料的回收。本文针对某车型车门外板材料利用率低的现状,通过采用废料利用方法,提升材料利用率,降低制造成本。
总体方案
如图1 所示,某商用车型冲压件车门外板由于产品造型原因,窗口废料被切除,零件材料利用率低,仅为47.3%。为提高材料利用率、降低生产成本,对车门外板窗口废料进行再利用。主要研究内容有:(1)利废零件确定;(2)工艺设计及优化;(3)废料在线自动收集;(4)利废零件调试。
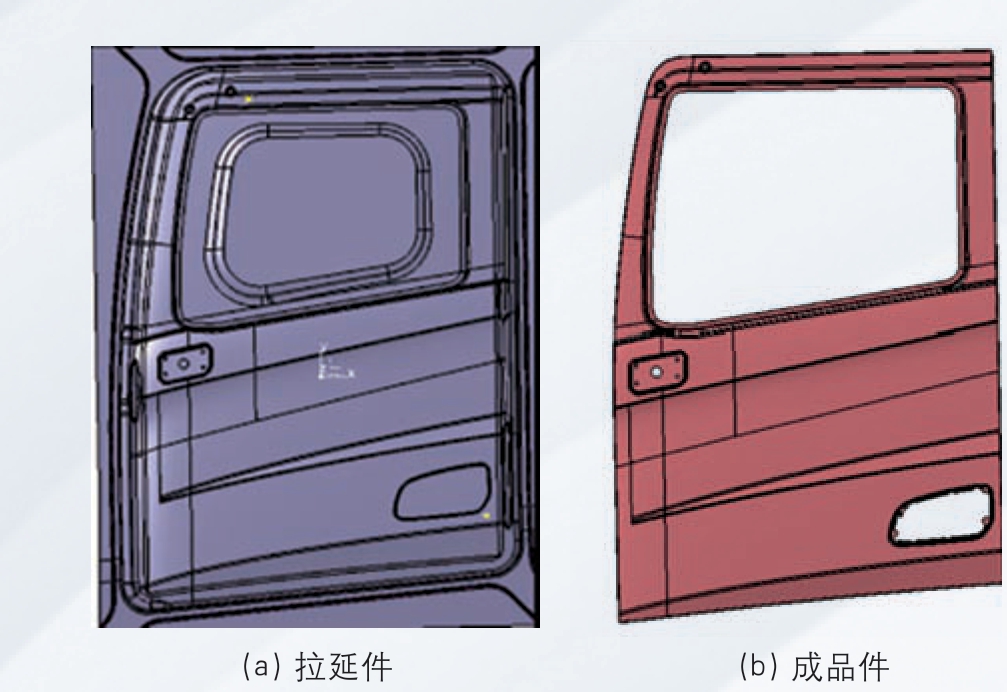
图1 车门外板拉延件与成品件对比
利废零件确定
为了选取合适的利废零件,需要保证车门外板窗口废料与利废零件的材料规格相同,零件尺寸适中。
利废零件梳理
车门外板的材料牌号为ST13,厚度为1.0mm,窗口的尺寸约为850mm×550mm。根据窗口的尺寸,从该车型111 种薄板冲压零件中筛选出6 种尺寸适中的零件。依据材料利用率最高及工艺性最优的原则,初步选择拟利废产品为车门加强板,如图2 所示。
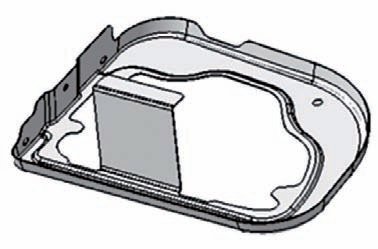
图2 车门加强板
材料规格更改
由于图2 的加强板材料牌号为ST12,厚度为0.9mm,与车门外板窗口废料的材料规格不一致,因此需要对车门某加强板进行产品更改。通过与设计部门研讨,经过CAE 分析验证,同意车门某加强板材料规格的变更,即将车门某加强板材料规格变更为ST13/1.0mm。由此最终确定车门某加强板为最终利废零件。
工艺设计和优化
废料收集后,通常需要根据利废零件的毛坯尺寸进行二次剪切。二次剪切不仅增加了人工工时,也会导致板料划伤。为解决上述不足,我们创新性的提出了车门外板窗口废料直接用作利废零件的毛坯、无需二次剪切的方案。为实现该方案,需要从利废零件工艺设计和车门外板工艺优化两方面开展工作。
利废零件工艺设计
在对零件的冲压成形过程进行分析时,需不断对板料轮廓进行调整,以达到利废零件成形性最优。图3 为利废零件的成形性分析结果,可以看出零件成形性较好,从而确定利废零件板料轮廓。
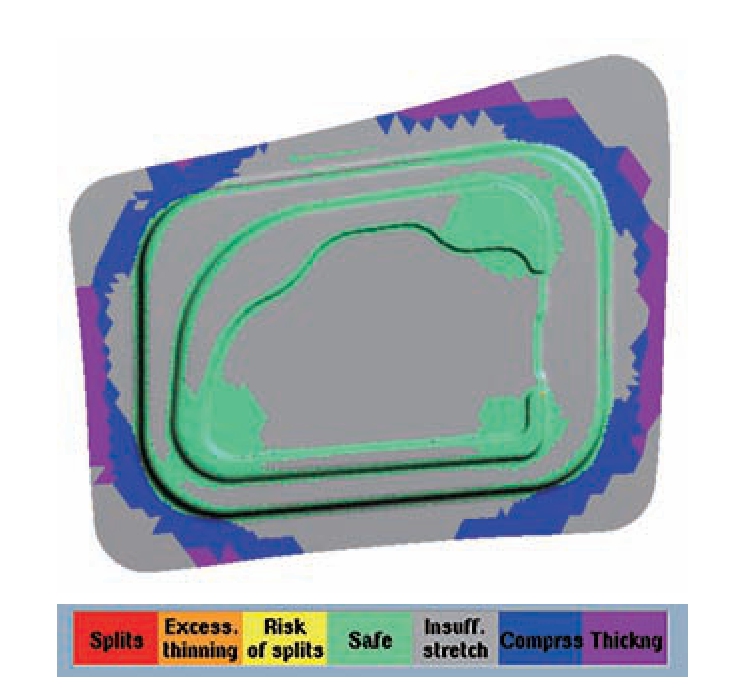
图3 利废零件成形性分析
车门外板工艺优化
(1)拉延模面设计。
根据利废零件板料轮廓,需要对车门外板窗口位置拉延模面进行设计;另外,车门外板拉延后窗口位置的材料变形率不能过大,以免影响利废零件的拉延稳定性,因此需对车门外板窗口位置的变形率进行分析。图4 为车门外板减薄率分析结果,窗口位置的减薄率在4%以下,即拉延后窗口废料的厚度约0.96mm,满足料厚(1±0.09)mm 的公差要求。
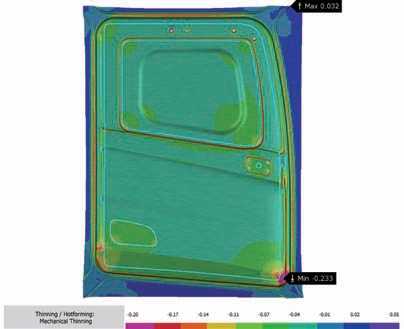
图4 车门外板减薄率分析
(2)废料切断工艺设计。
为保证车门外板生产过程中废料滑出顺畅,原有工艺方案如图5(a)所示,将工艺补充的废料切碎,但这种工艺方案使得车门外板窗口废料被切碎,无法完整的收集。为确保车门外板窗口废料的完整性,同时保证废料形状与利废零件板料形状一致,对原有工艺方案进行如图5(b)所示的优化。
(3)端拾器吸盘布置。
冲压自动线利用端拾器上的吸盘实现各序零件的传递。如图6 所示,预留窗口废料抓取的位置,保证废料抓取稳定可靠。
废料在线自动收集
自动线废料收集方式介绍
冲压自动线废料回收方式可分为线侧回收、线尾回收和线内回收三种。
线侧回收是指在模具废料出口增设皮带机,废料由皮带机传输到工作台外,该收集方式的缺点是新制皮带机的投入成本高、制造周期长,并且需对压力机安全门改造。线尾回收是指通过设计专门托料架,采用端拾器抓取废料到线尾,再进行人工收集的方式,该收集方式无法实现自动收集、堆垛。线内回收是指在自动线内工作台上放置废料回收装置,但该收集方式一般只能实现废料在线收集,不能实现自动堆垛。
废料在线收集装置的设计与实现
基于现有废料收集方式的不足,我们创新性的提出了车门外板窗口废料的在线收集、自动堆垛的方案,可提高自动化水平和劳动效率,避免人工码放的板料划伤问题。
(1)设计方案。
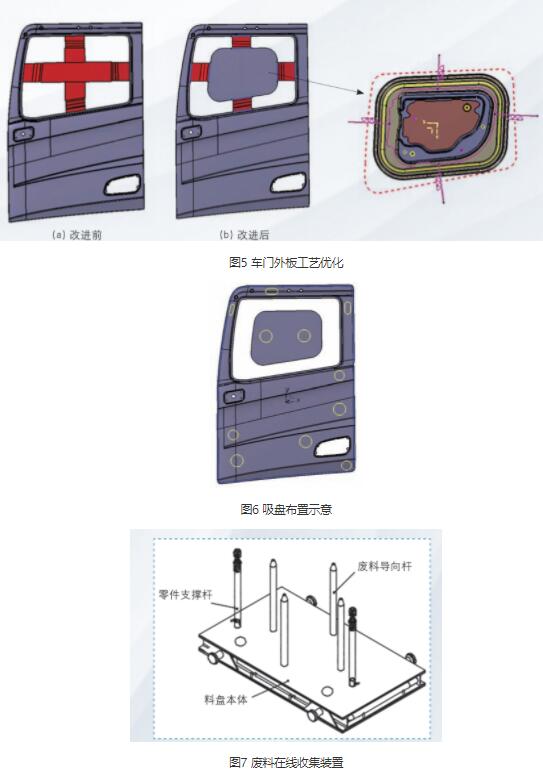
如图7 所示,该装置包括料盘本体、零件支撑杆和废料导向杆。料盘本体用于盛装废料,带有快速定位孔、零件支撑杆夹紧装置、废料导向杆安装孔和废料导向杆存放区。零件支撑杆,用于支撑冲压零件。顶端采用聚氨酯材质的支撑块,与支撑杆螺纹连接,可调节高度,以保证支撑块和零件稳固接触。为保证导向稳固、无晃动,零件支撑杆与料盘本体可用螺丝进行手动紧固。废料导向杆,用于保证废料片准确滑落到指定位置。杆顶端有斜度,用于导正废料。废料导向杆可快速安装于料盘本体的导向杆孔洞中,也可拆卸置于料盘本体四周的废料导向杆存放区。导向杆高度与线首毛坯板料数量一致,保证自动线线首换料和空工位废料装置拆卸同时进行,减少不必要的生产停歇。
(2)调试验证。
车门外板所在自动生产线为1×2000t+4×1000t 的压机组合方式,其工序内容为“拉延→修边冲孔→修边→翻边→空工位”,因此可将废料收集装置安装于空工位压机工作台上。通过现场调试和批量验证,实现了车门外板窗口废料的在线收集、自动堆垛,如图8 所示。
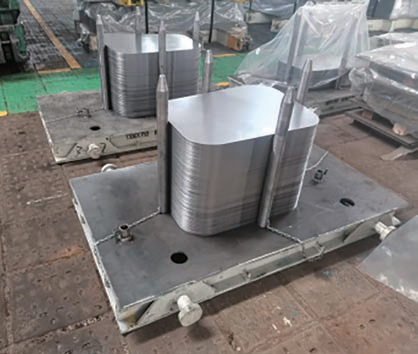
图8 废料收集装置实物
利废零件调试
调试问题描述
在利废零件实际调试过程中,出现图9 所示的翻边局部型面超差问题,影响下序装配。
问题分析及整改
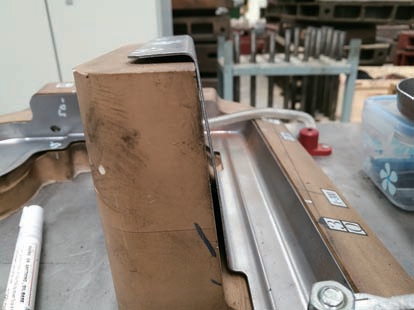
图9 利废零件尺寸超差
经过分析,由于窗口废料存在拉延硬化,二次成形后存在翻边回弹问题,尺寸精度控制困难。因此,可以在原产品上添加图10 所示的三角筋和竖筋,以控制翻边回弹,最终调试出合格零件。
总结
通过对车门外板窗口废料的利用,车门外板材料利用率由原来的47.3%提升至50.3%,单车节约成本18.2 元;若按年生产7 万辆计算,每年节约材料成本127.4 万元。
本文主要在两个方面提出了创新性方案:(1)针对废料收集后通常需进行二次剪切的不足,本次实现了车门外板废料直接用于利废零件生产,降低了人工工时,避免了板料划伤。(2)针对冲压专业内废料收集改造量大、自动化低的不足,本次设计了一种自动线在线收集装置,实现了车门外板窗口废料的在线收集、自动堆垛。该装置结构简单,易于实现,提高了自动化水平和劳动效率,避免人工码放的板料划伤问题。
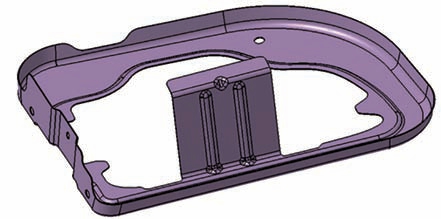
图10 利废零件产品更改
金键
冲压工艺工程师,主要从事商用车驾驶室冲压产品的生产准备及现场生产维护工作,并承担一汽解放全新J7 驾驶室白车身及保险杠工艺开发及产业化应用项目。
针对车门外板材料利用率低的问题,进行了车门外板利废工艺分析。通过从利废零件确定、利废零件及车门外板工艺优化、废料在线自动收集、利废零件调试等方面的努力,实现了车门外板窗口废料的再利用,提高了材料利用率、降低了生产成本。该方案创新性的实现了废料直接用于生产,无需二次剪切,减少了板料划伤;创新性的实现了废料的在线收集、自动堆垛,提高了自动化水平和劳动效率。