浅谈车门外板水切凹坑面品问题解决
文/刘斌,秦剑,陈绍毅·浙江吉智新能源汽车科技有限公司
汽车外观精细感知程度要求越来越高,对冲压单件也提出了前所未有的挑战,我司生产的一款车门局部光影不顺问题凸显,急需尽快整改。使用8D 的问题解决方法,组建多方论证小组,使用鱼骨刺图工具快速锁定问题真因,保证此问题快速解决,从而提升整车精细感;通过反省问题过程,制定预防对策,防止类似问题发生。
汽车保有量越来越大,为了提升整车产品的竞争力,板材外观精致感急需提升至完美状态。本篇文章以我司某款车型车门外板为例,以苛刻/质疑的眼光提出水切部位凹坑问题,并使用8D 的方法思路快速消除此问题,为今后解决此类问题提供参考。
问题描述
如图1 所示,某款车型前车门水切部位光影不顺,存在局部凹坑,整车精致感极差。通过手触/油石打磨板材单件,左右前门外板均发现对应部位面品凹坑,此问题单件/白车身Audit 评价定义为B 级。
原因分析
组建3 ~5 人的多方论证小组共同梳理左前门外板冲压过程,集中开展3 轮次头脑风暴,反复对过程变差因素讨论、现场过程跟踪确认,通过对人、机、料、法等几个方面识别过程中变差因素,使用鱼骨刺图工具进行罗列并排查影响,锁定问题产生原因,如图2 所示。
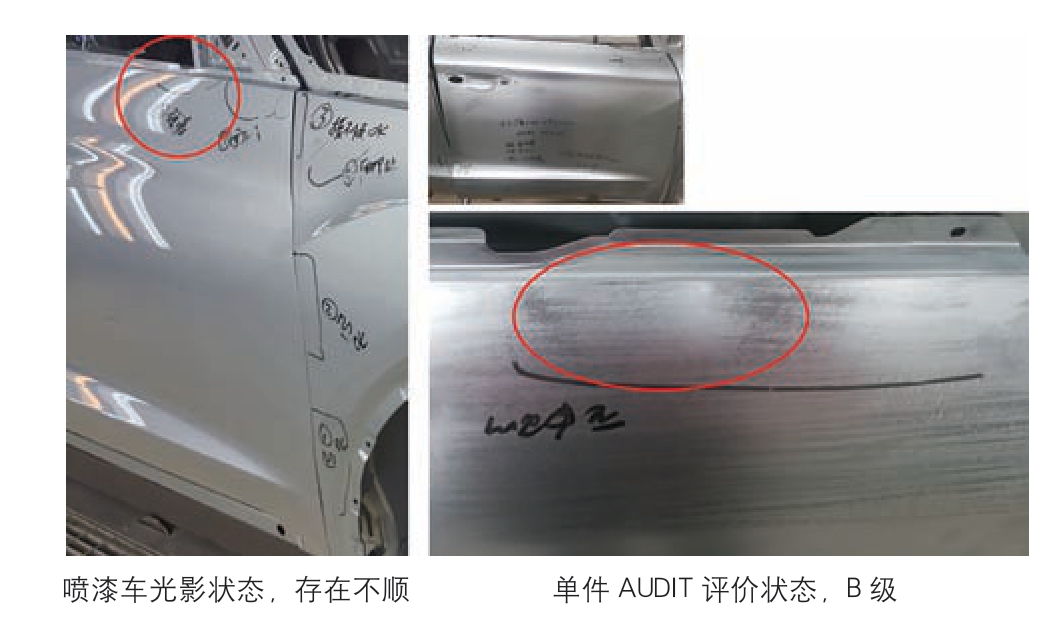
图1 实际问题
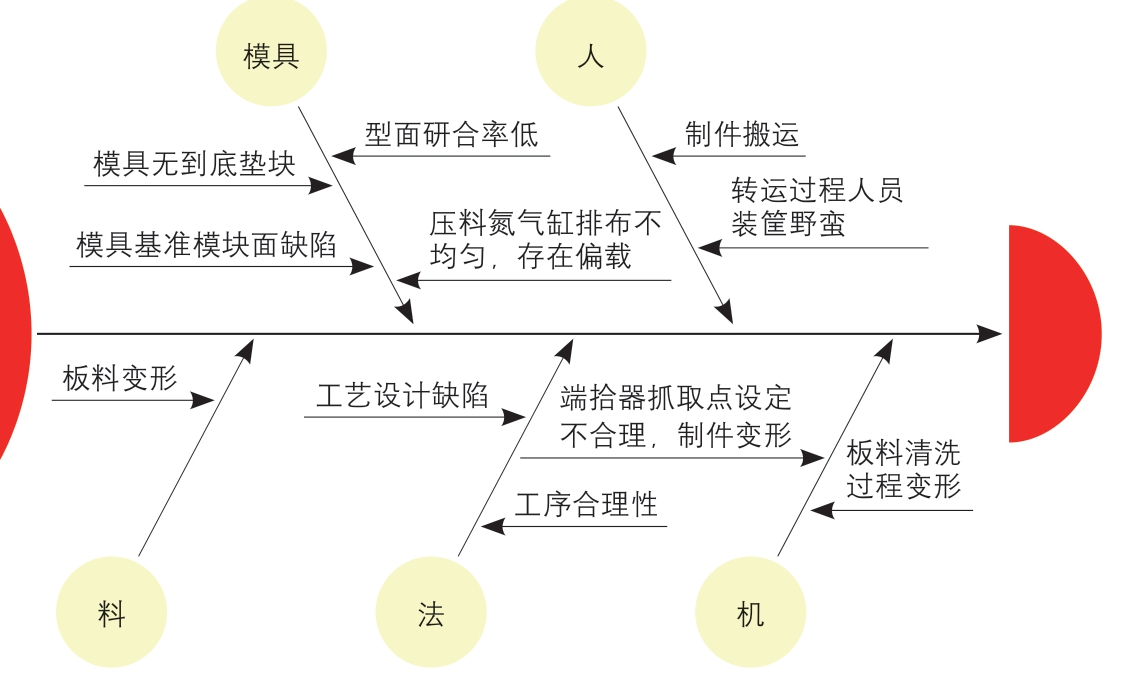
图2 鱼骨刺分析变差因素
因素筛查
通过鱼骨刺图工具识别变差因素,对识别的各个因素筛查如下。
(1)人员排查。
通过跟踪现场工作过程,对操作人员标准作业手顺/工位器具存放动作识别,确认无人为造成的制件面品凹坑问题。
(2)机械手排查。
主要对机械手取放件高度、吸盘位置、送件位置进行排查,要求取件高度控制在30 ~50mm、送件对中无明显偏移、吸盘符型无强制单件变形问题,通过对以上因素排查未发现问题。
(3)板料排查。
跟踪板料出库下料、转运上机、在线清洗输送、板料抓取等过程,确认板料出库到放置模具全程无变形问题。
(4)模具工艺/结构排查。
工艺成形过程排查:首先,车门外板工艺内容为OP10 拉延→OP20 修边→OP30 整形修边分离→OP40翻边,针对工序内容组织小组内讨论并明确工艺风险点。讨论结论为:缺陷部位翻边位置未拉延到位,在OP30 进行翻边整形,工艺排布存在风险。之后,通过对现场OP10 ~30 工序制件状态确认,OP10、OP20 均无面品凹坑,OP30 整形后单件对应位置问题复现,如图3 所示。
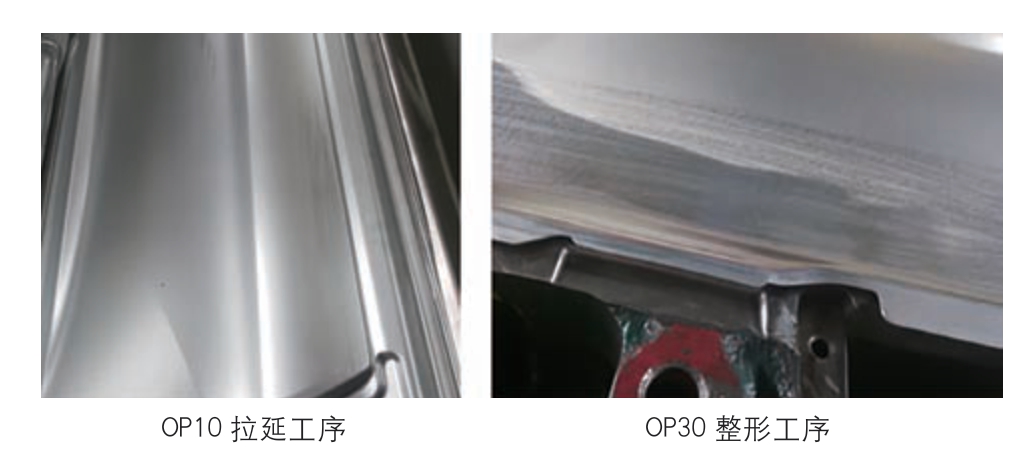
图3 OP10、OP30 对比
模具结构排查:(1)凸模基准确认。凸模基准对应位置型面排查,整体光洁、型面平顺,基准无问题。(2)压料板压力源以及垫块排布排查。工艺设计要求压力源、垫块均匀布置,对于受侧向力部位需设置防侧结构。通过对OP30 模具结构排查,压力源布置均匀,不存在偏载,并且产生缺陷部位设置有氮气缸及到底垫块(图4)。(3)压料板对应部位研合率确认。为消除翻边过程板料沿型面流动,压料板对应水切部位需保证强压效果,且研合率要求达到95%以上。将OP20 制件上下表面涂布均匀蓝油,放入OP30 模具型腔内,将闭合高度上调10 ~20mm,压机动作一次后查看上表面蓝油状态,通过以上排查发现研合率存在不均匀问题,如图5 所示。
原因锁定
通过以上筛查,车门外板水切部位凹坑问题原因锁定如下。
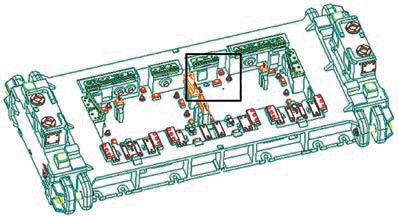
图4 OP30 模具结构
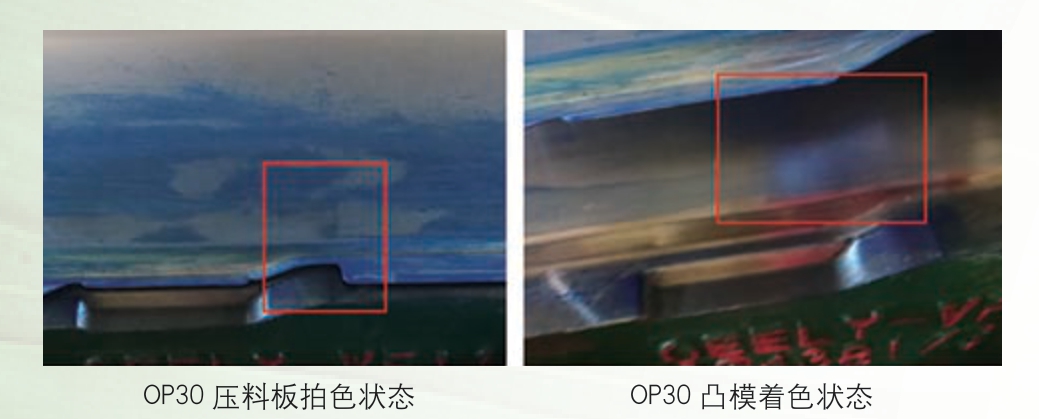
图5 研合率存在不均匀问题
(1)OP30 模具整形工序压料板研合不均匀,强压效果不良。
(2)工艺设计存在缺陷,参考现有成熟工艺,拉延采用浅成形+整形或一次拉延到位设计,由于工艺更改涉及长周期/高成本投入,不做纠正整改。
对策制定及实施
多方论证小组对问题真因剖析并结合以往整改经验,具体对策为。
(1)凸模基准部位进行冷补焊,凹坑部位做0.2mm 隆起,使板材呈现反变形趋势,对隆起部位手工修顺过渡。
(2)对OP30 缺陷部位压料板进行补焊,缺陷部位进行局部强压0.2mm 处理,调试压机粗研合去压伤,生产压机上进行精研调试出件,如图6 所示。
整改效果验证
通过以上整改措施,经过3 个班次生产稳定性验证,整改效果如图7 所示,前车门水切部位油石打磨连贯/手触无明显手感,每批次600 台份制件状态稳定一致,涂装涂漆后效果良好,达成预期更改目标。
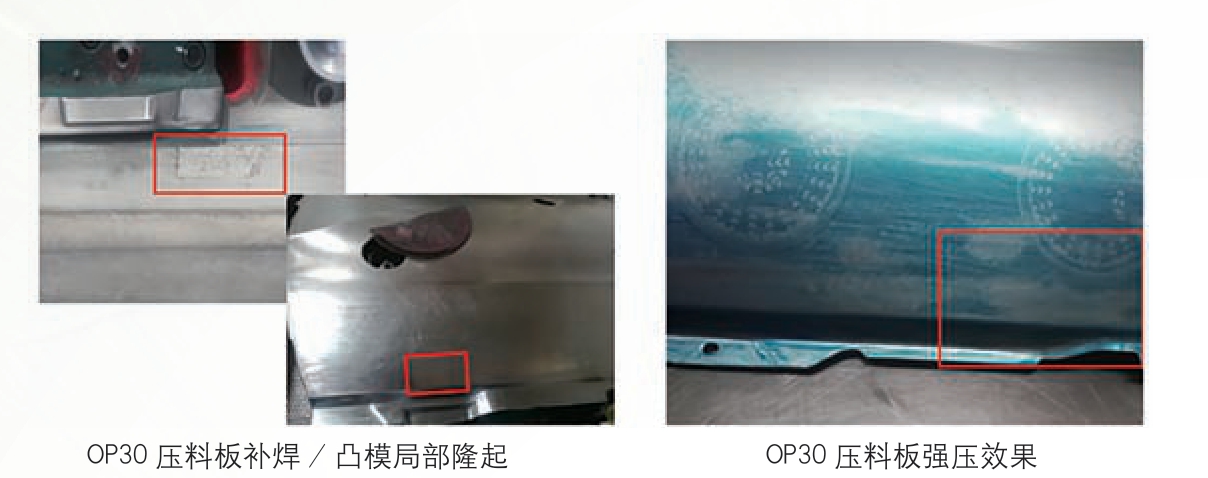
图6 具体对策及实施
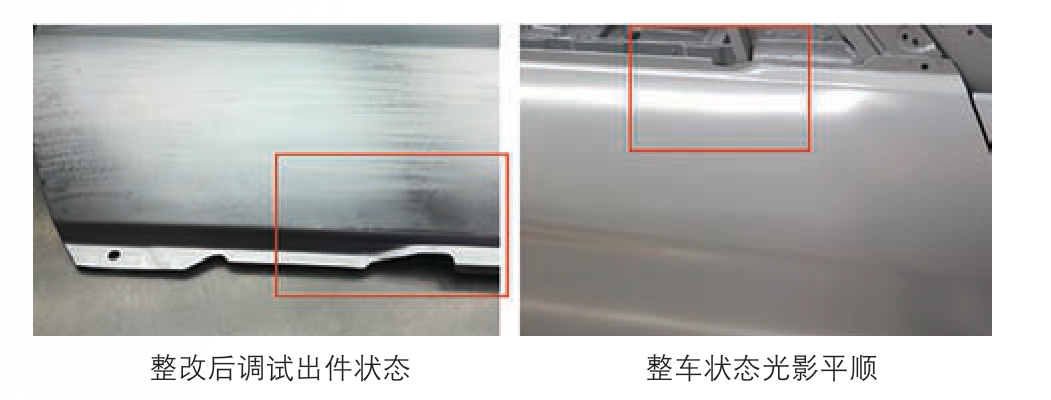
图7 整改结果
标准化及反省
为防止类似问题重复发生,问题管理实现PDCA管理,对我司车门外板开发过程标准化及反省进行控制。
(1)车门外板水切部位采用拉延一次到位或浅整形工艺,设计阶段即消除此类问题风险。
(2)模具加工数据审核阶段,水切部位作为点检项目,预留0.2mm 研合强压量,工艺阶段即开展问题预防,减少后期成本投入。
结束语
利用8D 的问题解决思路,组织多方论证小组开展头脑风暴,使用鱼骨刺图工具识别真因,最终找到了车门外板水切凹坑的问题原因,并制定实施了直接有效的整改方案,快速提升了单件及整车精细感。此外,8D 思路中还需考虑问题闭环管理,通过对问题解决过程反省,制定预防对策,完善标准化体系流程,防止类似问题的再次发生。
刘斌
主管工程师,主要从事汽车工程研发,并负责冲压量产模具的开发/交付、外协冲压件的供应商管理等工作,曾主持完成多款集团车型冲压ME 工作。
汽车外观精细感知程度要求越来越高,对冲压单件也提出了前所未有的挑战,我司生产的一款车门局部光影不顺问题凸显,急需尽快整改。使用8D 的问题解决方法,组建多方论证小组,使用鱼骨刺图工具快速锁定问题真因,保证此问题快速解决,从而提升整车精细感;通过反省问题过程,制定预防对策,防止类似问题发生。