智能折弯装备技术研究
文/王长福·安徽联盟模具工业股份有限公司
在当前工业转型升级过程中,钣金加工行业正朝着自动化、数字化、智能化、高速化方向发展。由于国内数控折弯机起步较晚,目前仍以人工换模为主,导致模具装配精度低、换模效率低、自动化程度低等诸多问题,与国外先进技术尚存在较大差距。
折弯机模具自动夹紧技术
传统折弯机夹紧装置(图1)通过螺丝紧固,在安装或更换上模时,需要松紧几十个螺丝,费时费力并需配备专用扳手,很不方便。不同机械夹紧装置夹紧力存在差异,夹紧力不一影响产品质量等问题,导致折弯机换模效率低。
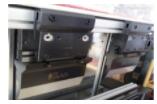
图1 传统上模夹紧装置
为了实现折弯机快速换模,公司设计开发了一体式液压夹紧装置(图2),该装置包括与折弯机连接的上模夹紧机构、产生夹紧力的液压系统。其中,上模夹紧机构包括夹具体、置于夹具体中的夹紧块、置于夹紧体中复位弹簧、置于夹具体前表面的前盖板、前盖板下方镶嵌标尺,以及置于夹具体后表面的后主盖板、后左端盖板、后右端盖板。
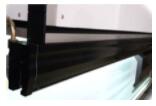
图2 一体式液压夹紧装置
夹具体下部开设有供模具装夹部位插入的方槽,方槽两侧面均开设有水平沟槽,方槽右侧面开设有圆孔,该孔内设置有与孔相配合的夹紧块。夹具体右侧面开设盲孔与螺纹孔,盲孔内置有复位弹簧,复位弹簧一端与夹紧块接触。夹紧块前端开设梯形状凸起,与模具的装夹槽形成紧密接触面并有效夹紧,夹紧块后端开设凹弧面,与耐压油管配合。前盖板的下部表面开设有沟槽,该沟槽中镶嵌有标度模具位置的位置刻度尺。后主盖板左侧面开设有半圆形圆弧槽,槽内置有耐压软管。
液压系统包括置于后主盖板中的耐压软管、置于后左端盖板中的油管接头、上端连接液压管路系统,液压夹紧装置的液压管路系统与折弯机数控系统完整对接。工作时,折弯机数控系统发出指令,液压泵给耐压软管注油,耐压软管瞬间充压胀开,挤压夹紧块,夹紧块瞬间夹紧折弯上模,从而实现快速自动夹紧折弯上模。反之,液压泵卸压,置于夹紧块中的复位弹簧推动夹紧块,夹紧块挤压耐压软管,耐压软管中液压油被挤出,耐压软管恢复扁平状态,夹紧块与折弯上模松开。
折弯机自动换模单元
为了实现折弯机器人自动换模,公司设计开发了适用于机器人装卸的智能折弯模具(图3)和专用机器人夹钳机构(图4)。智能折弯模具在模具本体上内置RFID识别芯片,并开设机器人卸装模具长孔和纵向凹槽,在凹槽内安装按钮等部件。夹钳机构由夹钳钩、夹钳本体、气缸、法兰、气管接头、接近传感器组成。夹钳机构工作时,气缸活塞杆顶出夹钳钩,机器人将夹钳钩伸进并穿过模具卸装长孔,夹钳钩内侧面超过模具按钮面,机器人抬高模具夹钳机构,夹钳本体端面贴紧模具表面,气缸活塞杆回缩,夹钳钩压紧模具按钮,接近传感器检测夹钳钩夹紧状态,并将夹紧状态信号反馈给机器人,机器人移动模具,实现模具装卸,如图5所示。
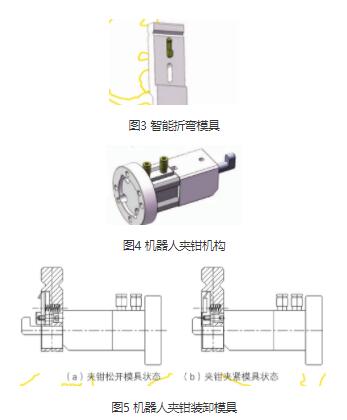
折弯机自动换模时,控制系统发出换模指令,液压系统接受指令后,液压夹紧机构动作松开。机器人接收指令后,通过射频识别技术识别模具,利用模具夹钳机构抓取识别的模具,并将其放置在折弯机液压夹紧相应位置,实现模具的自动装卸,如图6所示。在这个过程中,模具夹钳机构能否抓住模具主要靠夹钳上的传感器来探测。模具安装结束后折弯机开始折弯工作。同批次产品折弯完成后,控制系统再次发出换模指令,从而进入下一个工作循环。

图6 机器人装卸模具
在当前工业转型升级过程中,钣金加工行业正朝着自动化、数字化、智能化、高速化方向发展。由于国内数控折弯机起步较晚,目前仍以人工换模为主,导致模具装配精度低、换模效率低、自动化程度低等诸多问题,与国外先进技术尚存在较大差距。