冲压成形CAE 技术的现状与发展
文/苏传义,邰伟彬,任闯,代晓旭·中国第一汽车集团有限公司工程与生产物流部
近几年,随着计算机技术和模拟分析软件的迅速发展,冲压CAE 分析技术已经得到广泛应用,从产品开发、产品冲压工艺性分析、DL 图设计、模具调试,一直到冲压生产性问题的解决。通过模拟分析、虚拟制造,对整个过程进行分析,提前发现问题,分析原因,提出解决方案,进一步改善产品、优化工艺方案,创新工艺方案。因此避免了大量的设计、制造缺陷,提高了产品质量,节省了大量的时间,降低了开发成本。冲压CAE 方面的软件是比较多的,目前常用的专用软件有Autoform、Dynaform、Pam stamp。通用性软件有:MSC.MARC、ABAQUS、ANSYS-DYNA 系 列 等。本文通过一些具体的案例,运用Autoform 软件,介绍CAE 分析技术的应用,存在的不足及未来发展方向。
同步工程
产品冲压工艺性分析
通过CAE 分析判定零件的开裂、起皱、冲压负角、滑移线等缺陷状态,进一步优化产品。⑴零件不能有开裂、起皱现象(图1),否则需要更改产品。⑵产品不能存在冲压负角,需要优化。确定冲压方向后,软件自动计算出哪些地方存在冲压负角,并通过颜色显示出来。图2 所示的红色区域存在冲压负角。⑶某车型发罩外板拉延件的棱线在拉延过程中有5mm 的滑移线,但没有滑出圆角,满足工艺要求,如图3所示。
冲压工艺方案规划
通过全流程的CAE 分析,确定工艺方案,包括拉延、翻边、整形、修边和冲孔方向、回弹等,通过优化产品,缩短工序,减少模具数量,降低模具投资。
材料成本控制
⑴确定材料牌号。选择不同的材料,进行CAE 分析,对结果进行分析、判断,确定产品合适的材料牌号,降低材料成本。
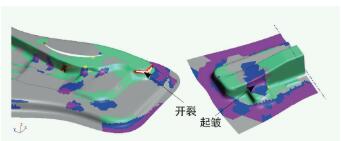
图1 CAE 分析判定零件的开裂、起皱
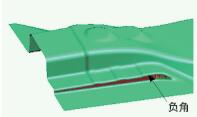
图2 冲压零件存在负角
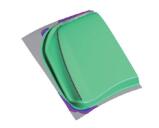
图3 某车型发罩外板拉延件棱线滑移
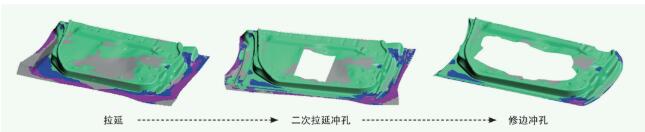
图4 冲压工艺方案规划
⑵优化板料排样。通过CAE 分析,优化排样,提升材料利用率,降低成本。某产品的拉延毛坯,料片是凹形形状,采用矩形板料落料工艺,该产品材料利用率为40.4%;现采用无废料排样落料工艺,该产品材料利用率提升到53.7%。
⑶废料利用。图5(a)为某车型全景天窗顶盖,图5(b)为拉延件修边后产生的天窗口废料,图5(c)为顶盖后横梁,图5(d)为顶盖后横梁拉延件,用天窗口废料作为板料。从模拟分析可以看出,此方案可行,顶盖的材料利用率由43%提升到50%。
冲压设备选择
⑴确定板料尺寸。通过CAE 分析,确定板料形状和尺寸,计算出模具大小,判断压机工作台尺寸是否满足要求。
⑵计算成形力。通过CAE 分析,计算成形力大小,从而确定冲压设备的吨位。某车型侧围加强板拉延件,抗拉强度590MPa,成形力1800t,压边力300t。
⑶通过全流程的CAE 分析,确定工序数量,选择合适的压力机生产线。
CAE 分析技术在冲压工艺设计中的应用
全流程的CAE 分析技术
图6 为某车型背门内板CAE 分析过程,对成形过程进行详细分析。分析拉延是否存在缺陷并进行优化,合理布置拉延筋,确定板料尺寸;判断修边冲孔方向是否合理;选择合理的翻边冲压方向;分析回弹状态等。
冲压工艺方案的创新
同一个产品可以有不同的冲压工艺方案,之间的差别十分显著。如果采用常规工艺方案,没有风险;如果采用创新的工艺方案,效益显著,但可能带来巨大的风险。此时非常需要进行CAE 模拟分析,对冲压工艺方案进行判断。
用成形工艺代替拉延工艺
⑴左/右连接板,形状对称,材料DC52D+Z-60 /60,料厚1.4mm, 常规冲压工艺方案,左右件对接,一模双件,拉延工艺。五道工序,分别为:拉延、修边冲孔、修边冲孔、翻边、侧翻切开。创新工艺方案,左右件对接,一模双件,成形工艺,三道工序,分别为:落料冲孔、成形、修边冲孔切开,如图7 所示。
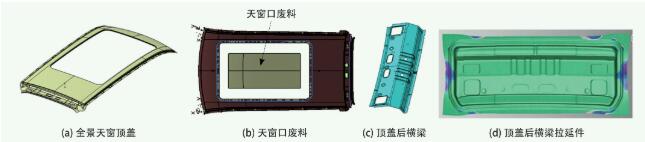
图5 废料利用
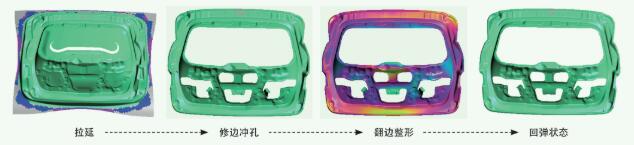
图6 某车型背门内板CAE 分析过程
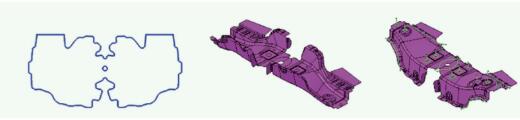
图7 创新工艺方案
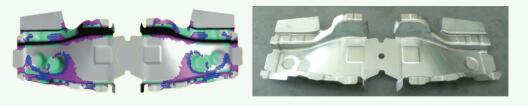
图8 CAE 模拟图和实际成形图
对成形工艺进行CAE 分析,主要针对成形工序进行分析,如图8 所示,没有起皱开裂的现象发生,图8 右图所示为实际生产的成形件,成形工艺方案取得了成功。采用新工艺,节省两套模具,模具结构也很简单,产品质量好,而且材料利用率提升6%。提高了产品质量,降低了模具投资,减少了材料成本、生产成本,效果十分显著。
⑵轿车背门外板上部、下部对接拉延工艺。背门外板上部、下部常规工艺方案,不在同一套模具加工,每个产品一般为4 道工序。为了降低投资,提高效率,创造性的提出轿车背门外板上部、下部对接拉延工艺,采用一张板料,4 道工序。图9(a)为背门外板上部、下部产品形状,图9(b)为背门外板上部、下部对接拉延件造型。通过CAE 分析,可以看到,没有产生起皱开裂的缺陷,滑移线在合理的范围内,没有产生冲击线,因此方案可行,已经批量生产。
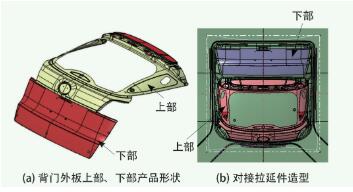
图9 轿车背门外板上部、下部对接拉延工艺
⑶汽车外表面件型面补偿技术。板材在成形后,一般都要发生回弹,特别是外表面件,由于形状平缓,结构强度弱,变形不充分,发生回弹。高强度板零件、铝合金板材成形后,回弹也比较大,尺寸超差严重,造成模具多次整改,成本很高。现在模具厂家试图通过CAE 分析进行回弹预测,通过回弹补偿技术解决这一难题,也有不少成功的案例。某轿车顶盖回弹补偿值和CAE分析结果,实际结果与分析结果比较接近,试模一次成功。
影响回弹的因素很多,有工艺、材料、凸凹模间隙、设备吨位、产品形状、模具制造精度等,型面补偿技术,目前多数模具厂家采用CAE 模拟分析和经验相结合的方式进行,还不够成熟,还没有完全改变多次试模的状态。
CAE 技术在模具调试中的应用
前门内板角部起皱问题的解决
图10(a)为前门内板起皱区域,(b)为产品加筋位置形状。角部拉延起皱,增大进料阻力,则开裂。最后确定更改产品,加筋吃皱、形状尺寸位置,既要考虑将皱吃掉,又要满足造型美观的要求。经过详细的CAE 分析,确定了产品加筋的形状位置,并且一次更改成功。
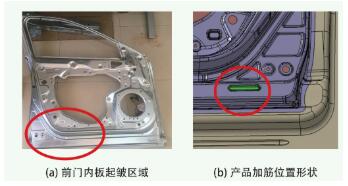
图10 前门内板角部起皱问题
某车型左右地板连接板成形起皱问题
该产品左右件不完全对称,左右件对接拉延成形后,在中间切开,图11 所示区域起皱明显。在中间工艺补充部分增加一条筋,经过CAE 分析,起皱消除。采用该方案,模具更改一次成功。
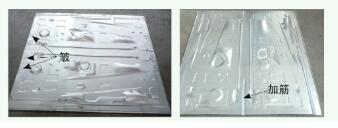
图11 左右底板连接板成形起皱
CAE 分析技术在内高压成形工艺中的应用
图12(a)为某轿车前副车架主管的产品形状,(b)为工艺流程图,(c)为CAE 分析的成形性,(d)为CAE 分析的管的壁厚分布。调试过程中出现的问题,与分析过程很接近,通过调整工艺参数,得到合格的产品零件,模具调试比较顺利,已经批量生产。
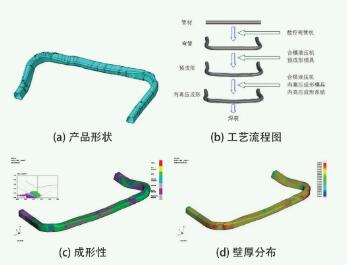
图12 内高压成形工艺
CAE 分析技术在热冲压成形中的应用
图13(a)为某车型前底板中通道,钢板厚度为0.9mm,材料为USIBOR1500P,(b)为CAE 分析模型,其中包括上模、下模和板料。(c)为CAE 分析的壁厚分布,(d)为热成形零件(激光切割前)。该零件在调试期间并没有出现开裂和起皱缺陷,调试过程比较顺利,已经批量生产。
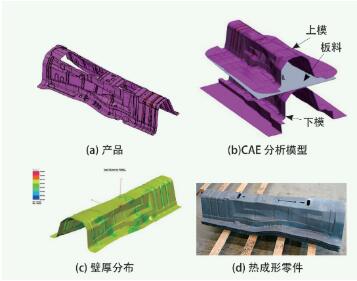
图13 热冲压成形工艺
结束语
以上通过一些实际的案例,介绍了CAE 分析技术在模具制造中的应用,我们可以看到,应用范围已经十分广泛,为模具行业的快速发展,起到了关键的作用。国内大型汽车覆盖件模具设计已经100%进行CAE 分析,优化工艺设计,提前规避风险,使调试问题越来越少,缩短了模具制造周期,提高了模具质量。随着汽车轻量化的要求,高强板、铝合金板的应用越来越多,如何解决回弹问题,已经是制约模具制造的瓶颈,如何克服这一难关,已经是摆在我们技术人员面前的一道难关。CAE 分析技术向着精确计算的方向发展,结合现场的成功经验,指导模具设计加工制造,仍是未来几年的发展方向。
近几年,随着计算机技术和模拟分析软件的迅速发展,冲压CAE 分析技术已经得到广泛应用,从产品开发、产品冲压工艺性分析、DL 图设计、模具调试,一直到冲压生产性问题的解决。通过模拟分析、虚拟制造,对整个过程进行分析,提前发现问题,分析原因,提出解决方案,进一步改善产品、优化工艺方案,创新工艺方案。因此避免了大量的设计、制造缺陷,提高了产品质量,节省了大量的时间,降低了开发成本。冲压CAE 方面的软件是比较多的,目前常用的专用软件有Autoform、Dynaform、Pam stamp。通用性软件有:MSC.MARC、ABAQUS、ANSYS-DYNA 系 列 等。本文通过一些具体的案例,运用Autoform 软件,介绍CAE 分析技术的应用,存在的不足及未来发展方向。