精冲技术研究现状及发展趋势
文/杨泽亚,杜贵江,李佳盈,彭群·北京机电研究所有限公司
杨泽亚
精密冲裁技术(简称精冲)是一种基于普通冲裁技术发展而来的塑性加工技术,采用齿圈压边,引入压边力和反压力,抑制冲裁过程中原材料的撕裂,使材料在分离前基本保持塑性变形,从而得到表面粗糙度低、尺寸精度高、断面质量好的精冲件。精冲技术具有加工效率高、加工周期短、绿色节能等优点,被广泛应用于汽车行业、航空工业、军工机械、电气设备等领域。
本文主要针对精冲技术生产中的实际问题,对精密冲裁技术的研究现状进行了归纳整理,并对精冲技术的发展趋势进行了分析与展望。
精冲技术研究现状
上世纪20 年代德国人Fritz Schiess-Forrer 通过试验研究发明了精冲方法并获得精冲技术专利,经过不断改进工艺方法和模具制造技术,于上世纪50 年代在欧洲进入了实际应用阶段。到目前为止全世界精冲机已经突破4500 台,零件种类接近10000 种。
进入新世纪之后,随着制造业的不断发展,零件的技术要求越来越高。为了满足精冲自动化、智能化、标准化的生产要求,生产出高精度、大尺寸、结构复杂的零件,相关学者对精冲机理、精冲工艺、精冲设备、模具等方面进行了全方面的研究。
精冲机理研究现状
区别于普通冲压过程,在精冲过程中材料的横向流动被齿圈压板抑制,变形区受到三向压应力,这使得在精冲接近完成时工件和原材料仍然保持为一个整体。因此,精冲过程中材料变形过程为塑性变形,在分离前基本不产生撕裂。
目前,精冲机理的研究方法主要是有限元分析和试验手段。研究对象主要针对精冲过程中的材料流动变化和加工效果,分析压边力、反压力、凸凹模间隙等加工参数对不同材料和精冲件质量的影响。有限元模拟技术的发展,为更加深入理解精冲机理提供了条件。通过有限元方法,能够得到材料及模具中剪切应力和塑性应变的分布,便于建立精冲力、模具和零件的关系。结合试验,可以对精冲过程进行分析,设定不同的边界条件,分析不同情况下的材料流动以及应力应变分布。
研究发现,增大压边力和反顶力能够有效提高零件表面质量。改变凸、凹模间隙和圆角半径主要影响零件剪切面质量。结合有限元方法,对V 形齿圈的角度、高度和位置与工件厚度的对应关系进行研究发现,精冲过程中变形区能够产生涡旋流动时精冲件质量较好。
目前对于薄板材料的精冲机理理论已经趋近成熟,但是对于一些齿面、厚板等特殊零件结构,仍旧需要进行相关研究。
精冲工艺方法研究现状
精冲工艺方法的提出主要是因为新的产品要求。面对高要求的零件,旧的精冲工艺不能满足产品要求,因此需要开发针对性的工艺方法。
闭挤式精冲工艺,利用前期挤压使材料径向流动,在冲裁过程前使废料区受到挤压变形从而封闭在模具型腔之内。封闭过程会使废料区预先产生塑性衰竭,导致精冲过程中基本不再产生径向变形,使变形区处于极大的三向压应力状态,提高材料塑性。闭挤式精冲工艺生产的精冲件没有毛刺,能够省去去毛刺的工序。闭挤式精冲工艺的开发降低了齿轮和链轮精冲的难度,并解决了厚板及低塑性材料在精冲过程中材料流动不足的问题。
精冲技术生产效率高、生产成本低,但是难以完成一些复杂零件的加工,为了解决这一问题,开展了精冲工艺与其他工艺复合的研究。精冲挤压复合成形工艺在理想的边界条件下,精冲变形与挤压变形相互独立,不存在相互作用,能够很好的完成凸台、沉孔等加工任务。
精冲设备及模具研究现状
精冲设备是决定精冲能力的重要因素之一,自1956年瑞士Schmid公司制造了第一台精冲机之后,精冲设备不断发展进步。我国精冲机通过进口和自主研发相结合,在普通冲压机上加装液压模架进行改造等方式进行开发研制。通过不断改进,在自动化、大型化上取得了很大进展。
精冲模具是精冲生产中最重要的部分之一,近几年来针对精冲模具的失效分析和寿命预测做了很多研究。图1 所示为一种典型的精冲模具。
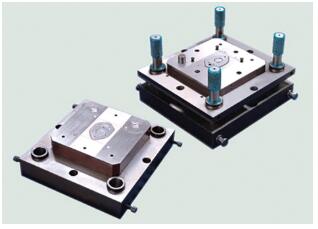
图1 典型精冲模具
精冲模具的研究方向主要分为三类:一是减少磨损、提高模具寿命,精冲模具工作环境恶劣,不可避免的受到磨损,为了延长模具使用周期,开展了一系列相关研究,主要利用有限元模拟等手段,改进模具参数,减少加工过程中的模具损耗。二是提高模具的智能化,通过检测模具使用过程中的各种参数以及模具工作区的残留情况,提高模具的耐用性,避免模具意外损坏。三是模具设计制造,针对新的加工工艺,设计面向该工艺的精冲模具,再根据有限元仿真模拟和加工实际效果对模具进行调整和改进。
精冲件产业化生产现状
自1965 年精冲技术被引进中国以来,我国精冲产业规模不断扩大,目前国内已有精冲企业70 余家。在材料方面,国内用于精冲的板料主要采用热轧原料+冷轧、球化退火,能够生产精冲用钢的企业众多,竞争激烈,但钢材质量上参差不齐。
随着人力成本增加,精冲生产线的自动化成为精冲行业发展的方向之一。精冲自动化生产线包括自动送料、送料位置检测、零件检测、物料管理、模具状态检测等部分。目前,自动送料机的研究和应用已经十分成熟,很多国内企业已经能够独立制造针对卷料的自动送料机。图2 所示为北京机电研究所有限公司研制的全自动精冲机。

图2 全自动精冲机
对于大批量生产的精冲零件来说,保证零件合格率十分重要,为了降低大批量精冲零件的检测难度,开展了很多精冲零件尺寸形状视觉检测的研究。基于精冲件的特征识别与视觉检测系统,开发了一系列用于检测零件缺陷的视觉检测设备,并根据精冲件的毛刺和缺陷特征,表面破损、划痕、压痕的图像特征,开发了相应的图像缺陷识别、分割与判别方法。
精冲技术发展趋势
传统齿圈压板精冲技术研究已经比较成熟,但为了应对更高的产品质量要求,进行了很多新工艺研发,新工艺和新技术的研究带来了相应的理论研究需求和设备需求。
从精冲件产业化生产实际来看,精冲技术未来主要有以下几个研究方向:
⑴智能化精冲生产。人力成本的增加使得精冲产业中对智能化、自动化生产,以及自动化排产的需求更加迫切。
⑵创新精冲技术方法。随着产品要求的提高,高质量、大尺寸、高精度的复杂零件,对精冲方法和精冲技术提出了更高的要求。
⑶实用的有限元模拟技术。有限元仿真技术给精冲技术研究带来了很大便利,但对于零件生产而言,精冲件后续的热处理、表面涂层工艺会严重影响零件尺寸,对零件从精冲到后续加工完整流程的仿真过程仍旧需要开展进一步的研究。
智能化精冲生产
精冲生产的自动化已经初见成果,瑞士Feintool公司生产的自动化精冲设备已经能够完成从上料、精冲到下料的生产过程,我国也自主研制了自动化精冲生产线并投入实际生产。但是根据精冲加工的生产流程,精冲生产线的自动化还需要考虑到生产排产的智能化,在设定生产计划之后,应当能够自动对原材料进行出库管理,以便于精冲加工。在实际生产中,精冲件排产、去毛刺、检验等工序目前仍依赖人工操作。
对于去毛刺等工序的自动化研究进展缓慢,大型精冲零件可以采用数控机床沿零件边缘去除毛刺,但面对小型大批量零件,尚未出现较好的可以替代人工的去毛刺加工方法。
因此,精冲智能化生产主要发展方向是对精冲生产线的整合以及个别工序的自动化研究,通过提高每个工序的自动化水平,完成智能化精冲制造要求。
创新精冲技术方法
自精冲技术出现以来,为了满足不同的制造需求,发明了很多实用的创新型精冲技术。传统精冲加工方法只能加工薄板类简单零件。为了解决厚板的精冲问题,先后出现了对向凹模精冲,往复成形精冲、挤压精冲等加工方式;为了避免压边圈对零件造成影响,研发了平面强力压板精冲技术;为了能够减小精冲零件的毛刺高度,形成光洁的冲裁面,开发了负间隙精冲方法。
随着制造业的发展以及制造要求的复杂化,对精冲生产的要求也越来越高。为了加工一些结构特殊的零件,以及满足更多的生产需求,创新的精冲方法是未来应当继续研究的方向之一。
实用的有限元模拟技术
由于精冲模具价格高昂,制作周期漫长,开展精冲试验研究十分不易。为了研究精冲加工中的各种工艺参数和应力应变情况,有限元模拟技术被大量使用。但有限元模拟技术的研究仍旧停留在对精冲过程中的零件和模具分析上,仅对工艺参数的调整和模具设计起到了帮助。
对于精冲件的生产过程来说,其在精冲工序结束后还需要经历去毛刺、热处理以及表面处理等多道后续工序。其中一些工序对精冲件的尺寸和形状会产生很大影响,某些零件在经过后续工序加工之后尺寸和形状可能无法满足图纸的相关技术要求。
目前,对于整个零件生产周期的模拟研究少之又少。设计开发能够对精冲件完整生产周期进行计算、仿真、控制,集成塑性变形、热处理和表面处理等模块的有限元仿真软件是未来研究的方向之一。
结束语
本文从精冲机理、精冲工艺方法、精冲设备及模具、精冲产业化生产等四个方面介绍了精冲技术的研究现状,根据精冲技术面临的问题和困难,简述了当前的解决方案并进行了分析。根据精冲产业生产效率高、生产成本低的技术特点,以及零件愈发复杂的需求状态,对精冲技术未来的发展趋势进行了展望,阐述了智能化精冲生产、创新精冲方法、精冲有限元模拟技术的重要性。
主要从事精冲工艺、精冲设备及精冲模具研究。
精密冲裁技术(简称精冲)是一种基于普通冲裁技术发展而来的塑性加工技术,采用齿圈压边,引入压边力和反压力,抑制冲裁过程中原材料的撕裂,使材料在分离前基本保持塑性变形,从而得到表面粗糙度低、尺寸精度高、断面质量好的精冲件。精冲技术具有加工效率高、加工周期短、绿色节能等优点,被广泛应用于汽车行业、航空工业、军工机械、电气设备等领域。