罗仁平:一位“技术控”的行业情怀
文/郭晓心·FM 记者
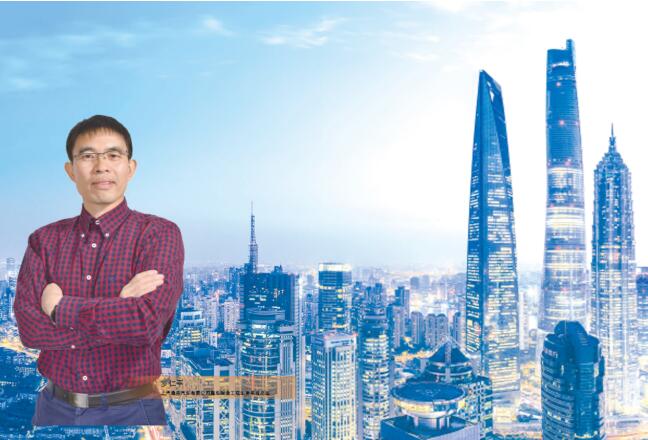
罗仁平 上汽通用汽车有限公司整车制造工程车身系统总监
众所周知,2019 年以来,我国汽车产业已经进入低速增长、高质量要求阶段,汽车产业全面变革时代的到来,将给汽车行业带来更多的机遇与挑战。如何适应协同、创新、突破,加快汽车行业转型升级,全面提升行业核心竞争力,把握智能化、网联化发展趋势成为汽车行业的一种必然选择。
冲压作为汽车制造的四大工艺之一,汽车行业现状及未来发展必然对汽车冲压行业产生深刻影响,为了探寻汽车冲压行业的历史与变迁,解开行业同仁的从业困惑,《锻造与冲压》杂志记者有幸采访到上汽通用汽车有限公司(以下简称“上汽通用”)整车制造工程车身系统总监罗仁平先生,请他为我们解读汽车冲压技术的难点、热点问题以及汽车冲压行业未来的
与冲压结缘
说到与冲压行业的缘分,罗仁平笑称,能进入冲压行业比较偶然,但这其中又蕴藏着必然的因素,一切还得从读书的时候谈起:“1989 年,我考入大学,所学专业为化工过程机械,这与冲压完全没有关系。大学毕业后,也就是1993 年,我踏入硕士研究生阶段并被安排学了力学专业,这三年对力学的专研,为我后来从事冲压行业的工作提供了很大帮助,因为冲压成形中涉及的变形分析正是以力学研究为基础的。1996 年,我迈入博士研究生阶段,这一年正值上汽通用成立,在听取师兄建议后,我选择了材料加工为博士阶段的研究方向,1999 年博士毕业后,我顺利入职上汽通用,开始在冲压车间从事模具维修和生产运行相关工作,经过七年的历练后,于2006年离开冲压车间到整车制造工程部担任高级经理,负责同步工程阶段的冲压工艺开发与项目管理工作。可以说,从我毕业到现在为止的20 多年的时间里,从未离开过冲压行业。”据了解,罗仁平还担任上海市模具协会常务理事,每年都会参加协会组织的各类技术交流活动,与行业同仁及相关配套供应商分享技术经验,共同推动行业进步。
从国产化中突围
谈及冲压技术的发展,罗仁平思索道:“它源于上世纪二十年代汽车的工业化生产,在开始的很长一段时间里,由于缺乏理论及计算机技术的支撑,成形分析都是基于经验的判断。直到上世纪八十年代各种理论的不断丰富以及有限元技术的发展,成形技术才从经验走向科学。
国内汽车行业初始发展阶段,模具和设备主要依靠进口。面对高昂的价格及高傲的姿态,我深切感受到掌握冲压核心能力的重要性、必要性及紧迫性。要掌握冲压核心能力就必须走冲压设备和模具的国产化之路,同国内的相关供应商共同成长。作为国内汽车的领头羊企业,我们义不容辞地走上了模具和设备的国产化之路。2004年我们开始了模具国产化,从简单的地板模具,到复杂的侧围模具;从钢板模具,到铝板模具,我们克服了重重困难,成功地实现了国产化,在降低成本的同时,我们和供应商的核心能力也得到了培养和提高。2007 年我们开始了压机国产化,从国内首条国产化连续高速线项目,到国内首条全伺服冲压线项目,均成功地达成了预期目标。这两个项目都纳入了国家高档数控机床与基础制造装备科技重大专项工程,相同类型的压机线也成功地进入国际市场。将来,我们会不断关注冲压领域的创新并引入新技术、新装备,不断扶持国内冲压装备制造商,敢做第一个吃螃蟹的人,与模具、设备供应商协同成长。”
提及冲压工艺开发,罗仁平表示:“在项目前期同步工程阶段对零件的潜在风险进行识别,避免在项目实施阶段修改模具带来的成本增加和项目周期延误。除了常规的成形模拟及成形缺陷的识别,我们还开发了零件线末重力变形仿真、检具变形仿真以及机械手轨迹仿真等,识别更多的潜在风险。在项目前期同步工程阶段对仿真软件的依赖度很高,但目前大部分整车厂使用的成形仿真软件多为进口,工艺开发也主要依赖工艺经验的积累,如何实现仿真软件国产化以及提高软件的智能化程度也是非常重要的研究方向。”
热点难题待突破
提及汽车行业的节能环保,车身轻量化技术是一个绕不开的话题,众所周知,铝板和高强钢是主要的车身轻量化材料,在保证整车安全性能的同时有助于减轻整车重量,节约能源,提高耐腐蚀性。“实际上,铝板的冲压工艺和车身连接技术较钢板而言都要困难很多,全铝车身技术并不是一个轻松的课题。”略作感慨后,罗仁平深入地谈到:“从冲压工艺角度而言,由于铝板的弹性模量只有钢板的1/3,导致铝板的回弹要比钢板大很多,尺寸难以控制,因此在铝板模具制造过程中要保证模面饱满圆润、过渡光滑,避免扭曲回弹;制定补偿方案时要综合考虑全工序零件的回弹,挑选合适的尺寸拟合方案,确定适合的回弹补偿方案。从车身连接技术而言,车身连接大多采用焊接方式,但是由于铝板易氧化、导热率高、熔点低等原因导致铝合金可焊性差,以使用较多的点焊而言,各整车厂采用的铝板点焊方式都不尽相同。随着钢铝混合车身的发展,铝与铝、铝与钢的连接成为了迫切需要解决的难题。”
“随着国家对新能源汽车政策的不断更新,各整车厂都在加紧对电动汽车的研发。”紧接着,罗仁平继续说道:“以C-NCAP 为例,纯电动汽车和混合动力汽车都增加了电器安全考核项,包括碰撞之后的电压、电能安全及电解液是否泄漏等。电池盒和常规的大型汽车冲压覆盖件相比,电池盒本身形状不算复杂,材料还是常规的钢板或铝板材料,所以冲压的难度并没有提高多少,但是电池盒尺寸较大,内部加强件多,焊接引起的变形是一大问题,如何有效解决焊接变形成为车身制造过程中亟需解决的难题。”
智能制造从工业创新开始
“众所周知,制造业是国民经济的主体,如何提振制造业,实现智能制造成为必然选择,那么,作为制造业从业人员的我们首先要明白为什么要发展智能制造。”罗仁平引人入胜地阐释道:“自金融危机以来世界各国均面临市场需求萎缩、产值下降等困境,而大数据、云计算、物联网的兴起给各国制造业带来新的转型思路。各国都将发展智能制造作为战略核心不断推动制造业向数字化、网络化、智能化发展,向绿色化、服务化转型。2015 年我国推出《中国制造2025》,全面推进制造强国战略实施。各企业也根据国家政策做出相应的企业发展规划,对智能化的发展和创新的投入也不断加大。
我们要清醒的认识到,智能制造绝对不是一个概念,其实现需要踏踏实实一步一步完成。详细需求厘清、知识获取、算法选择、代码生成、系统调试,等等,少了任何一小步都不行。智能制造会在很长一段时间内不断发展成熟,绝不可能一蹴而就。
智能制造才刚刚起步,其终点还很遥远,未来仍有很多需要探索的地方,对应到行业企业就要持续保持创新能力,首先是要营造良好的创新氛围,培养员工的创新价值观。通过不断强调创新的重要性,来加强员工对合作、创新的认知,要给予员工合理的试错机会,对员工的建议给予足够的重视,对创新成果给予适当的奖励等,让创新不断地融入员工的日常工作中。其次是提供创新的平台,给员工提供一些创新相关的讲座和培训机会,让员工学习创新思维,提高创新思维能力,并建立相应的系统、平台等,让每一位员工的创新想法都能够被大家看到。”
技术无可替代
“在人类最基本的生活需求中,行是非常重要的一部分。在民用飞行器等更先进的交通工具量产之前,汽车仍然是当今社会人类出行的重要工具。”罗仁平分析道:“中国是全球重要的汽车生产和消费市场,2018 年中国汽车销量2808万辆,占全球近三分之一的汽车市场。相比于欧美日韩等发达国家汽车市场的2 ~3 家主流车企现状,像德国的奔驰、宝马和大众,美国的通用、福特、克莱斯勒,我国汽车工业仍然处于分散的水平,车企分化加剧,中国汽车行业的集中度有望加速提升。2018 年全国汽车保有量2.4 亿辆,千人保有量约172 辆,相较于美国780 辆/千人,日本587 辆/千人,我国目前的千人汽车保有量还有一定的发展空间,而且从各省分布来看,国内各地发展不平衡,东部、中部、西部保有量存在一定差异,长期来看中国的汽车行业还存在一定的增长空间。”
“对于冲压行业来说,随着各大主机厂车型的更新换代,汽车冲压件的需求也不断增加,而低成本、高效率的冷冲压依然具备很好的前景。”谈到这里,罗仁平解释道:“冲压技术更多的是跟随新材料和新工艺的变化而发展的,在新材料方面,铝合金和高强钢已经有一定的应用经验,但是镁合金、碳钎维等其他新材料的成形方式完全有别于常规冲压成形,在这些材料大规模应用之前,冷冲压仍然是制造汽车车身零件的主要方式;在新工艺方面,特种成形工艺和3D 打印等一些新工艺的出现丰富了制造选择,但是受制于成本、效率、质量等影响,目前基于模具的冲压技术在大规模生产中依然不可取代。”
结束语
采访的最后,提及整车市场对冲压技术发展的影响,罗仁平表示,随着人们审美水平的不断提升,汽车造型设计越来越复杂,这就需要冲压行业从业人员在工艺和模具设计方面不断创新,在实现设计意图的同时,更能满足消费者不同的审美需求。如今,车企为提升新车在市场上的竞争力,对如何缩短模具制造周期、降低生产成本以及提高生产质量等冲压技术不断提出新要求,促使了汽车冲压技术不断朝着数字化、智能化方向发展。
众所周知,2019 年以来,我国汽车产业已经进入低速增长、高质量要求阶段,汽车产业全面变革时代的到来,将给汽车行业带来更多的机遇与挑战。如何适应协同、创新、突破,加快汽车行业转型升级,全面提升行业核心竞争力,把握智能化、网联化发展趋势成为汽车行业的一种必然选择。